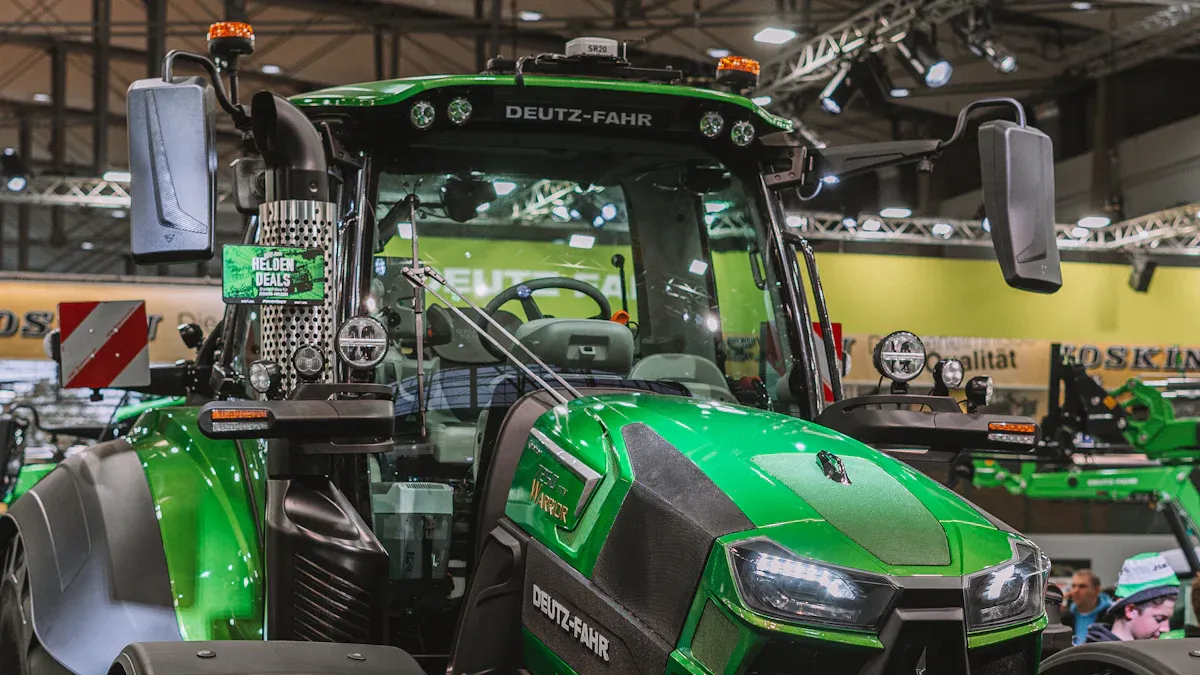
Custom and OEM casting solutions are very important for making agriculture machinery casting parts. Good castings make machines last longer and break down less. This helps farming equipment handle heavy work and sudden hits. New materials and careful design make machines work better. They also help save money on repairs and make machines last longer. KEMING is a trusted maker. They give strong parts that work well for today’s farms.
Key Takeaways
- Strong casting parts help farm machines last longer. They also help machines work better in hard conditions. – There are different casting methods like sand, die, and investment casting. These methods fit many parts and needs. – Picking the right material helps parts fight wear and rust. It also helps them handle heavy use on farms. – OEM casting saves money by making fewer parts. These parts fit better and make less waste. – Choosing a skilled casting partner with good technology is important. Good support gives strong and high-quality parts.
Common Casting Methods for Agricultural Parts
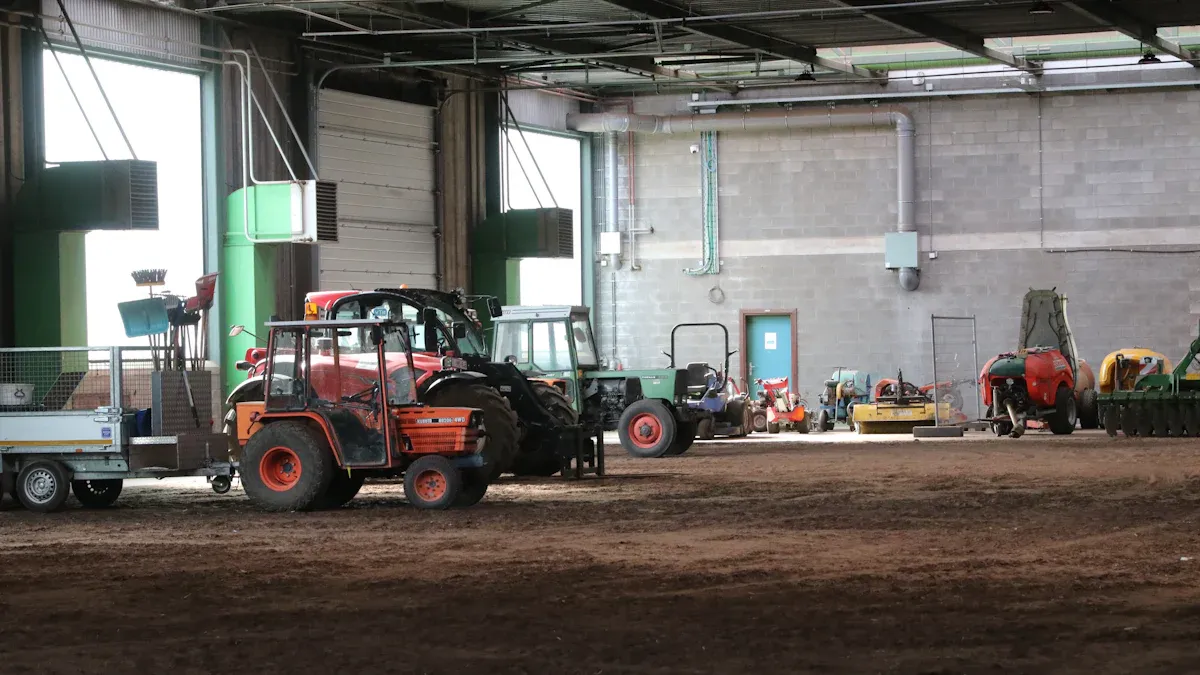
Casting is important for making strong parts for farm machines. Companies use different casting methods to make parts for modern farming. Each way has special benefits for certain parts and needs.
- Sand Casting
Sand casting is the oldest and most common method. It is good for big, heavy parts like engine blocks and plough bodies. This method works with many metals, like iron and steel. Sand casting is cheap for small batches. - Die Casting
Die casting makes lots of parts that are very exact and smooth. Companies use it for aluminum or zinc alloy parts, like gear housings and clutch covers. Die casting helps make machines lighter and use less fuel. - Investment Casting
Investment casting makes small, detailed parts with tight fits. It is great for tiny parts that need special shapes and smooth surfaces. This method can put many features in one mold. It can also add logos or product IDs. - Centrifugal Casting
Centrifugal casting is best for round parts like brake drums and wheel hubs. This way makes strong parts with few inside problems. These parts last long under heavy use. - Shell Moulding
Shell moulding uses sand with resin to make parts smoother and more exact. Companies use this for small parts, like valve bodies and bearing caps.
Note: Big companies use these casting ways for tractors, harvesters, and tillage tools. Many now pick die casting for better accuracy and to help the planet. New things like 3D printing and robots make parts even better.
Comparing Advanced Casting Methods
Companies pick between investment casting, lost foam casting, and lost wax casting for special farm parts. Each way has its own good points:
- Investment casting is good for small, tricky shapes with smooth surfaces. It uses materials again and makes tight fits.
- Lost foam casting is better for bigger parts and lots of pieces. It uses foam and sand, so it costs less for big orders.
- Lost wax casting makes very detailed and smooth parts. It is best for small to medium, fancy parts.
Aspect | Lost Foam Casting | Lost Wax Casting |
---|---|---|
Pattern Material | Foam | Wax |
Mold Material | Sand | Ceramic shell |
Process Complexity | Easier molds, fewer steps | Harder and takes more work |
Surface Finish | Good, but not as smooth as lost wax | Great, makes fine details |
Production Volume | Cheaper for lots of parts | Good for small to medium amounts |
Cost | Lower for big batches | Higher for work and materials |
These casting ways help companies make strong, exact, and low-cost parts for farm machines everywhere.
Agriculture Machinery Casting Parts
Typical Casting Components Used in Agricultural Machinery
Agriculture machinery casting parts are very important for farm machines. They help machines work well and last longer. KEMING makes many cast parts for hard jobs in the field. These parts can handle heavy work and tough weather. The most common cast parts are:
- Engine blocks and cylinders – These parts are strong and can take a lot of heat. They help engines work well even when it is hot or busy.
- Gearbox housings – These are made from steel or aluminum alloys. They keep gears safe and help power move smoothly.
- Axles and frames – These are made from iron or steel. They hold up heavy machines and do not bend or break easily.
- Hydraulic components – Pumps, valves, and cylinders help tractors and harvesters lift and move things.
- Brackets, structural frames, and transmission elements – These parts make machines stable. They also connect different machine parts.
- Cutting and soil-working tools – Blades, tines, and moldboards are cast to be strong and last a long time.
KEMING uses special casting ways like investment casting, shell casting, lost foam casting, and lost wax casting. These ways help make parts with tricky shapes and smooth surfaces. This means less extra work is needed to finish the parts.
Surface treatments like shot blasting, polishing, and heat treatment make agriculture machinery casting parts stronger and better looking. These treatments help parts last longer in rough places.
Applications of Casting Components in Various Types of Agricultural Equipment
Agriculture machinery casting parts are used in many types of farm equipment. Tractors need cast engine blocks, axles, and gearbox housings to be strong and work well. Harvesters use cast frames, hydraulic parts, and cutting tools to work with hard crops and soil. Planters and seeders use special cast seed metering housings and drive wheels. These help plant seeds in the right way.
The material picked for each part changes how it works. The table below shows what materials are used and why:
Material | Performance Characteristics | Common Uses in Agricultural Machinery |
---|---|---|
Carbon Steel | High strength, toughness, cost-effective | Blades, tines, structural components |
Stainless Steel | Corrosion resistance, durability | Pump valves, fasteners, connectors |
Manganese Steel | Wear resistance, high impact strength | Crusher jaws, hammers, wear plates |
Grey Iron | Good machinability, vibration damping | Gearbox housings, brake drums |
Ductile Iron | High strength, good ductility, corrosion resistance | Pivots, clutch pins |
KEMING picks the best material for each part. This makes sure every agriculture machinery casting part is strong, lasts long, and works well.
Benefits of OEM Agricultural Machinery Casting Solutions
Durability and Performance
OEM casting solutions make farm machines last longer and work better. Makers use strong materials like spheroidal graphite cast iron, ductile iron, and alloy steels. These materials help parts resist wearing out and handle strong hits. They also help stop shaking and can take a lot of pressure.
- Strong cast iron helps final drive housings and axles last longer.
- Making parts with close fits keeps out dirt and water.
- Special coatings and paints stop rust and help parts last longer.
- Machining the castings makes sure parts fit well and work smoothly.
- New casting ways like die casting and vacuum casting make parts that wear out less.
OEM casting solutions are trusted by top equipment makers. These parts can handle tough jobs and heavy use in the field.
Cost Efficiency
OEM casting solutions help save money for farm machine makers in many ways.
- Making one big part instead of many small ones costs less.
- Investment casting uses less metal and needs less cutting, saving time and tools.
- Die casting makes lots of parts fast and cheaper than welding or sand casting.
- Using iron castings instead of welded steel makes building easier and shipping cheaper.
- Iron castings last longer and need fewer repairs, so companies save on storage and paperwork.
These ways help machines break down less and last longer. Makers can spend more on new ideas and less on fixing old machines.
Design Flexibility
OEM casting solutions let makers design special parts for farm machines. They can make tricky shapes and parts for special jobs.
- Custom pump bodies made from 304 and 316 stainless steel work well for fertilizer pumps.
- Carefully made cast pump parts help irrigation systems and sprayers work better.
- Casting can make parts from 0.05kg to 100kg using different methods.
- Good materials stop rust and wear in tough places.
- Makers use many steps like tool design, testing, cutting, and heat treatment to meet high standards.
- Water glass and silicon sol casting, plus lots of cutting, make parts very exact and easy to change.
This helps makers build parts that fit special needs and make machines work better.
Equipment Compatibility
OEM casting solutions make sure parts fit many kinds of farm machines. CNC machining helps make parts that match each machine’s needs. Makers follow world rules like AISI, BS, JIS, and GB to make sure parts are good quality. Careful checks make sure every part is just right. Samples and drawings help give correct prices and make custom parts. Special teams help design and change products for different machines. OEM and ODM services let makers change parts so they fit many types of farm equipment.
Casting Process for Agricultural Machinery Components
Design and Prototyping
The casting process starts with careful planning and making models. Engineers use special computer programs to design the parts. They make models to test how the parts will work. CNC machining, 3D printing, and vacuum casting help make these models. This step helps find problems before making lots of parts. By testing models, companies make sure the parts will work well on farms.
Material Selection
Picking the right metal is very important. Engineers choose ductile iron, gray iron, stainless steel, or carbon steel. They pick based on what the part needs to do. Ductile iron is strong and bends without breaking. Stainless steel does not rust and works well in wet places. The best material makes the part last longer and work better.
Manufacturing Methods
Companies use different casting ways to make strong parts. The main steps are:
- Mold Preparation: Workers make a mold that looks like the part.
- Pouring: They pour hot metal into the mold.
- Cooling and Breaking: The metal cools and gets hard. Workers take off the mold to get the part.
- Finishing: They clean, cut, and treat the part to make it just right.
KEMING uses special ways like investment casting, shell casting, and lost wax casting. These ways help make tricky shapes and smooth parts that fit well.
Quality Control
Quality control checks every part to make sure it is good. Workers look at molds to see if they are right. They check the metals to make sure they are strong. They use X-rays and sound waves to find hidden problems. Special machines check if the part is the right size. Workers keep tools working well and are trained to spot mistakes. These steps make sure the parts are strong and ready for hard farm work.
Tip: Careful quality checks at every step help stop mistakes and make farm machines last longer.
Choosing a Casting Partner
Experience and Certifications
A good casting partner has many years of work and important certificates. They know how to make strong parts for farm machines. They check materials and parts at every step. Their teams use customer drawings to plan how to make parts fast. If a company has ISO 9001:2015, it means they care about quality. This certificate helps them follow rules and make sure parts are strong. Top companies also use special tests to find cracks and weak spots. These steps help make parts that last a long time on the farm.
Capabilities and Technology
The best casting partners use new machines and have skilled workers. They use metal machining and different casting ways like investment casting and die casting. These methods help them make tricky shapes and close fits. They use computer tools to design and check for mistakes. They also offer surface treatments like sandblasting to make parts stronger. Automation and 3D printing help them work faster and better. Companies that try new things can make parts that help farms do more work.
Support and Service
Great support and service make top casting partners stand out. Their sales and engineering teams help customers from start to finish. They give custom solutions and can make small or big orders. They help pick the best materials and ways to make each part. After-sales help includes tech support, warranties, and quick delivery. They also help with shipping to save money and keep parts safe. These services make sure customers get good parts with little waiting.
Supplier Evaluation Tips
When you look for a casting supplier, remember these tips:
- Work with makers to get expert help and save money.
- Check parts for surface problems and if sizes are right.
- Look for ISO 9001 and awards to see if they are trusted.
- Make sure they have the right machines and can make enough parts.
- Check if they offer help after you buy, like warranties.
- Visit their factory to see how they check quality and train workers.
- Ask for samples and test them for strength and fit.
Picking a partner like KEMING, who has lots of experience, good machines, and strong support, helps your farm machines work well.
Custom and OEM casting solutions help farm machines last longer. Good iron castings do not wear out fast. They can take heat and shaking. This makes machines work longer and break down less. Many companies now want more exact, green, and smart ways to make parts. Picking a skilled company like KEMING means you get good checks, new tools, and strong help.
- Strong castings help machines work better and save money.
- Skilled partners help farms work faster and earn more.
KEMING is ready to give special, trusted casting parts for today’s farms.
FAQ
What types of agricultural machinery parts does KEMING produce?
KEMING makes many different casting parts for farm machines. These include gearbox housings, engine parts, hydraulic parts, frames, brackets, and soil-working tools. Each part is made to be strong and last a long time.
How does KEMING ensure the quality of its casting parts?
KEMING follows ISO 9001 rules to make sure parts are good. The team checks raw materials and makes sure molds are correct. They test finished parts by looking at them and using special tools. This helps every part work well and be safe to use.
Which materials can KEMING use for custom casting orders?
KEMING uses stainless steel, carbon steel, alloy steel, grey iron, ductile iron, and aluminum alloys. The team picks the best material for each part. They think about what the part will do and where it will be used.
How can customers request a custom casting solution from KEMING?
Customers send drawings or samples to KEMING’s engineers. The team looks at what is needed and suggests the right materials. They give a price and help from start to finish. KEMING makes sure the whole process is easy and quick.