You cannot use most investment casting molds again. The process uses ceramic molds that are thrown away after casting. These molds break off the metal part when finished. Using each mold only once helps you get very detailed parts. This is different from permanent mold casting, where you can use the mold again. The materials and high heat make it hard to reuse molds. You should know these things before picking this casting method.
Key Takeaways
- Investment casting molds are made from ceramic. They break after one use. This helps make detailed and exact parts.
- Permanent mold casting uses strong metal molds. These molds can be used many times. This saves money when making many parts.
- Recycling wax and ceramic in investment casting helps cut down waste. It also saves important resources.
- New technology like 3D printing helps investment casting. Stronger mold materials make the process faster and lighter. It also makes it more efficient.
- Investment casting works best for small batches or tricky shapes. Other methods are better for making lots of parts with reusable molds.
Investment Casting Molds
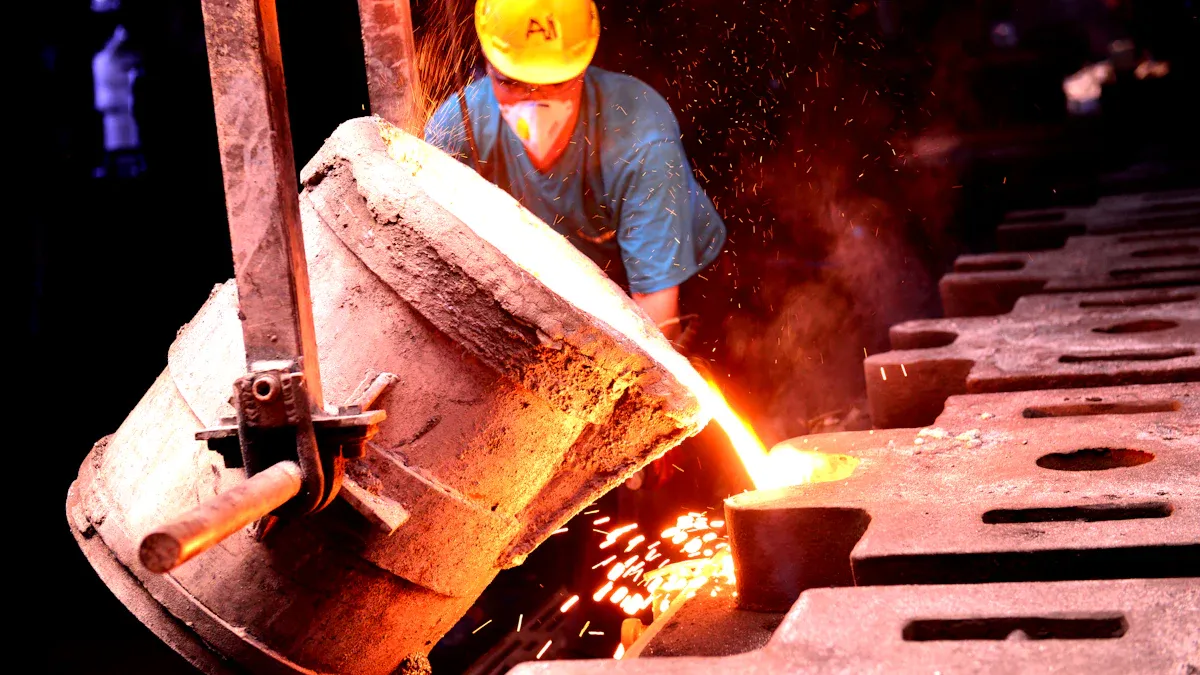
Disposable Molds
Investment casting uses disposable molds to make detailed parts. These molds are made from ceramic. Workers build the mold around a wax pattern. They melt the wax out before pouring in metal. When the metal cools, they break the ceramic to get the part. The mold cannot be used again because it breaks.
This method lets you make shapes that are hard to make with other methods. In 2024, the investment casting market was worth $17.2 billion. Many industries like cars, planes, and medical tools use this process. They need parts that are strong, light, and exact. This process also cuts down on waste and saves time on extra work.
Note: Disposable molds help you get smooth surfaces and tiny details. That is why many high-tech companies use this process.
Wax Pattern Reuse
The first step is making a wax pattern for each part. Most of the time, you use the wax pattern only once. But new studies show you can sometimes use wax patterns again. Scientists tested dewaxing up to 12 times with autoclave and microwave methods. They found that microwave dewaxing keeps the wax better. The wax stays cleaner and keeps its shape, so you can reuse it more.
Here is a table with some important results:
Dewaxing Method | Wax Quality After 12 Cycles | Contamination Level | Reuse Potential |
---|---|---|---|
Autoclave | Lower | Higher | Limited |
Microwave | Higher | Lower | Improved |
You can see that microwave dewaxing helps recycle wax better. This makes the process greener and can save money.
Reusable vs. Disposable
Permanent Mold Casting
You may wonder how permanent mold casting is different. Permanent mold casting uses molds made from steel or cast iron. These molds are very strong and last a long time. They can be heated and cooled many times. You can use the same mold to make thousands of parts. This is good for making lots of the same part. The molds help lower the cost for each part you make.
- Permanent mold casting uses strong steel or iron molds.
- These molds can make many parts with good accuracy.
- The molds are tough and can be used again and again.
- You get smooth surfaces and exact shapes.
- This method is great for making many parts and saving money.
Tip: Permanent mold casting is best if you need many parts that are all the same.
Why Investment Casting Uses Disposable Molds
Investment casting uses molds made from ceramic and wax. You have to make a new mold for every part. The mold breaks when you take out the finished part. The ceramic shell cracks open to get the metal part out. You cannot use these molds again.
Why do you need new molds each time in investment casting? It is because you need very fine details and exact shapes. The ceramic molds can show tiny details and thin walls. You can make shapes that are hard to make with permanent molds. This process works with many metals, both ferrous and non-ferrous.
Here is a table that shows the good and bad sides of disposable molds in investment casting:
Performance Metric | Advantages of Disposable Molds (Investment Casting) | Disadvantages of Disposable Molds (Investment Casting) |
---|---|---|
Dimensional Accuracy | Very exact sizes | Hard to make holes smaller than 1.6 mm |
Surface Quality | Smooth surfaces; no lines where parts join | N/A |
Material Compatibility | Can use many types of metals | N/A |
Detail and Complexity | Can make thin parts with lots of detail | N/A |
Cost Implications | Less extra work needed after casting | High cost; patterns and molds can only be used once |
Pattern Reusability | N/A | Patterns and molds cannot be used again, so more waste |
You can see that investment casting gives you very exact and smooth parts. But you have to pay more because you cannot use the molds or patterns again. This makes investment casting better for small batches or special shapes.
Note: Investment casting molds are used only once because they must break to get the part out. This helps you make tricky shapes and fine details, but it also means higher costs and more waste.
Factors Affecting Reuse
Mold Materials
You should think about what the molds are made of. In investment casting, molds use ceramic and special binders. These materials help make smooth and detailed parts. But they do not last for more than one use. The ceramic shell breaks when you take out the metal part. This makes it almost impossible to use the mold again.
Here is a table that shows how different materials affect how well molds work and if you can use them again:
Material Component | Composition / Type | Role in Mold Reusability and Performance |
---|---|---|
Wax Patterns | Natural or synthetic wax, fillers, additives | Additives help control shrinking and make patterns stronger, but you can only use them once. |
Ceramic Shell Binders | Alcohol-based or water-based (colloidal silica) | Water-based binders last longer, but the shell still breaks after casting. |
Refractory Fillers | Fused silica | Makes the mold stable and heat-resistant, but does not let you reuse it. |
Additives | Various | Help make the surface smooth and easy to remove, but do not let you reuse the mold. |
Even with strong fillers and binders, the ceramic shell cannot be used more than once. The materials in investment casting are picked for detail and accuracy, not for making the mold last longer.
Casting Process
The way you cast also changes if you can reuse a mold. In investment casting, hot metal is poured into the ceramic shell. The high heat and pressure make the shell crack. This is needed to get the finished part out. You cannot use the same shell again.
Other casting methods use metal molds that last much longer. These molds can handle heat and stress for many cycles. Here are some important things about the process that affect if you can reuse the mold:
- Metal molds in other methods can be used thousands of times.
- Pouring temperature, preheating, and cooling time are important settings.
- High production rates and smooth finishes help metal molds be reused.
- In investment casting, the ceramic shell cannot handle being heated and cooled over and over.
Note: If you want to use molds again, pick a process that uses metal molds, not ceramic ones.
The cost for each part depends on how many times you can use the mold. In investment casting, you need a new mold every time, so each part costs more. This process gives you great detail, but you cannot reuse the mold.
Recycling and Sustainability
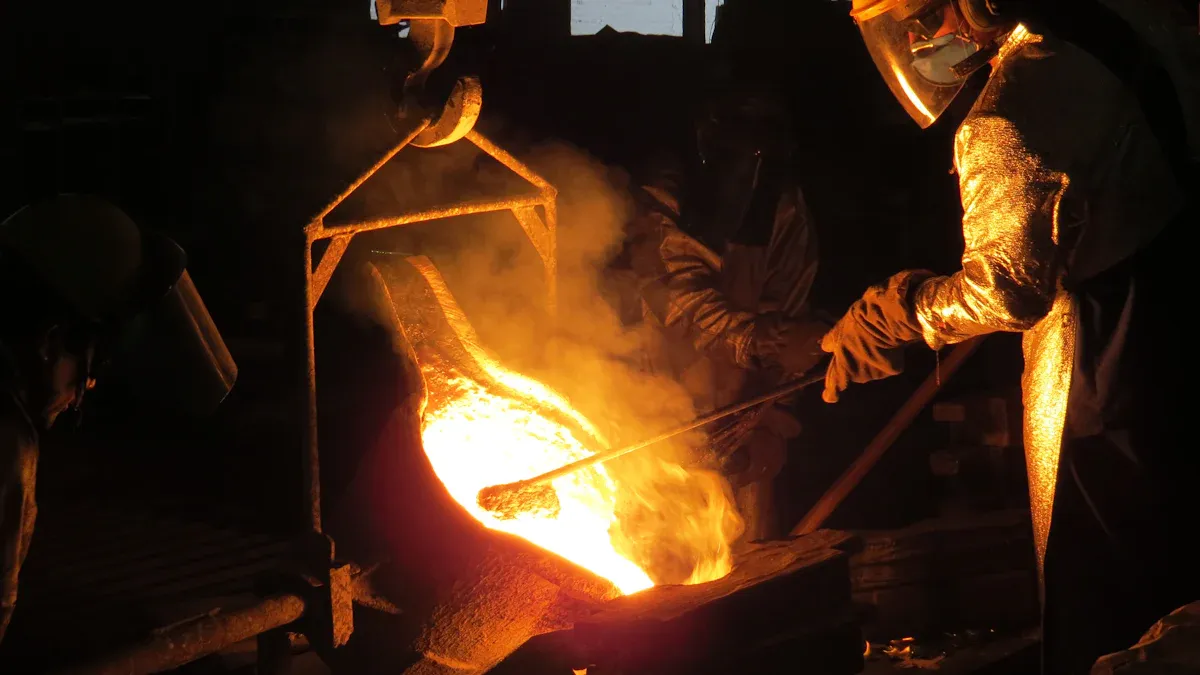
Ceramic Material Recycling
You help make investment casting better for the planet. When you use ceramic molds, you make waste each time. But you can recycle a lot of this ceramic material. Foundries use different ways to get sand and ceramic back from old molds. Here is a table that shows how these ways compare:
Treatment Process | Efficiency Highlights | Quality of Recovered Material | Economic Aspect |
---|---|---|---|
Wet Mechanical Treatment | Gets green molding sands back well | High | Not as good for saving money |
Dry Mechanical Treatment | Saves the most money | Medium quality | Best for saving money |
Dry Mechanical + Thermal Treatment | Mixes both ways for better results | High | Good for saving money |
Dry mechanical and thermal treatments give you good recycled sand. This helps you make less waste and save natural resources. Waste sand from investment casting has minerals like mullite and cristobalite. These minerals make the recycled sand good for new molds or other heat-resistant products. If you treat the sand under 1500°C, it is safe and good for the environment.
♻️ Recycling ceramic materials helps you send less to landfills and save raw materials.
Wax Recovery
You can also get wax back and use it again in investment casting. After melting out the wax pattern, you can collect and clean the wax. This step helps you make less waste and spend less money. New dewaxing methods, like microwave dewaxing, keep the wax cleaner and stronger. This means you can use the wax more times without losing quality.
Being sustainable in investment casting is more than just recycling. Melting metal uses a lot of energy—up to 2,000 kWh for each ton of metal. Melting can be 74% of the total impact on the environment in casting. By recycling metal scraps and using energy-saving tools, you help use less energy and lower your carbon footprint. Some foundries reuse up to 90% of their sand, so they need less new material.
🌱 When you recycle wax and ceramic, you make investment casting better for the planet and save money.
Modern Techniques
3D Printing in Investment Casting
3D printing helps make patterns and molds for investment casting. This technology lets you create hard shapes fast. Many companies use 3D printed patterns to save time and money. This is helpful for small orders or custom parts. For example, Tech Cast made a 300-pound part for Sulzer Pumps in four weeks. 3D printed ceramic cores and SLA patterns give smoother surfaces and more exact parts.
Here are some real results from using 3D printing in investment casting:
- You do not need permanent tooling, so you save money on small jobs.
- SLA-printed patterns help make big parts, like 30-inch impellers, with better quality.
- Customers get parts faster and with better strength.
- Aerospace companies made parts up to 47% lighter by using 3D printed patterns.
Case Study / Metric | Description / Result |
---|---|
Channel Fitting (Airbus A400M) | Design changes and 3D printing made the part 17% lighter. |
Hinge Arm (Comac C919) | Using 3D printed patterns made the part 47% lighter. |
Aerospace TiAl6V4 Part | Energy use dropped from 1090 kWh/kg to 266 kWh/kg; CO2 emissions fell from 650 kg/kg to 127 kg/kg. |
🚀 3D printing helps you make parts faster, lighter, and with less waste.
Innovations in Mold Materials
New materials make molds stronger and last longer. Adding nylon fibers to ceramic shells makes them thicker and stronger, especially at sharp corners. This helps the mold handle more stress and crack less during casting. You also need fewer coating layers, which saves time.
SLA 3D printing gives patterns with very fine detail, up to 10 micrometers. This means molds can show tiny features and have smoother surfaces. Nanomaterial-reinforced metals make molds stronger and work better. These metals can handle more heat, which is good for aerospace.
Studies show nylon fibers in ceramic shells make edges 40% thicker. This helps the mold fill better and lowers the chance of mistakes. You get better and more reliable parts.
AM Process | Materials Evaluated | Molded Part Material | Key Findings / Improvements |
---|---|---|---|
MJT, MEX | Digital ABS, Fullcure 720, Ultem1010 | PP | Better shrinkage control and part quality |
MJT, PBF-LB/M | Digital ABS, bronze alloy (DM20) | PP | Improved heat and strength performance |
MEX | Ultem1010 | PP | More uses per mold, longer tool life |
🧪 New mold materials and 3D printing help you get stronger, more exact, and more efficient investment casting results.
You cannot use molds again in investment casting. This process uses ceramic molds only one time to make detailed parts. Recycling wax and ceramic helps cut down on waste and saves materials. New methods, such as 3D printing, help make the process faster and better. If you want to use molds more than once, try other casting methods. Many studies show that systems like Mivan or aluminum formwork save money and time when used many times. These choices are good if you want to save money and reuse molds for a long time.
FAQ
Can you reuse investment casting molds?
You cannot use investment casting molds again. The ceramic shell breaks when you take out the metal part. This lets you make detailed shapes. But you need a new mold for every part.
Why do you use ceramic molds in investment casting?
Ceramic molds can take very high heat. They also show small details well. Ceramic molds help you make hard shapes that other molds cannot.
Is investment casting better for small or large batches?
Investment casting works best for small or medium batches. Making a new mold for each part costs more money. Large batches usually use other casting methods.
Can you recycle materials from investment casting molds?
Yes, you can recycle some wax and ceramic materials. Many foundries clean and use wax again. Some also treat and reuse ceramic sand to help the planet.
How does investment casting compare to permanent mold casting?
Investment casting uses ceramic molds only one time for detailed parts. Permanent mold casting uses metal molds that last for many uses. Pick investment casting for tricky shapes. Use permanent mold casting for making lots of the same part.