Servicios de torneado CNC a medida
KEMING se especializa en servicios de torneado CNC personalizados, ofreciendo una gama completa de operaciones de torneado, tecnología avanzada y mano de obra experta. Si usted necesita prototipos o producción a gran escala, KEMING entrega confiable, rentable, y soluciones que trabajan a máquina de la precisión adaptadas a sus requisitos exactos. Nuestros servicios incluyen:
- Torneado CNC personalizado: KEMING puede producir piezas personalizadas adaptadas a especificaciones exactas, manejando geometrías complejas y tolerancias estrechas.
- Versatilidad de materiales: Trabajan con más de 50 tipos de metales y plásticos, lo que permite a los clientes seleccionar el mejor material para su aplicación.
- Precisión y calidad: Utilizando avanzados centros de torneado CNC y operarios cualificados, KEMING garantiza una alta precisión y una calidad constante en cada lote.
- Entrega rápida: Con una programación eficiente y modernas máquinas CNC, KEMING puede suministrar piezas rápidamente, dando soporte tanto a prototipos como a series de producción.
- Opciones de postprocesado: Ofrecen servicios de acabado adicionales, como anodizado, recubrimiento en polvo y embalaje personalizado para satisfacer requisitos específicos de los clientes.
- Operaciones complejas: Las capacidades de torneado CNC de KEMING incluyen procesos multioperación como roscado, taladrado y torneado cónico, lo que permite la producción de piezas complejas en una sola configuración.
- Certificación ISO: Como empresa con certificación ISO 9001, KEMING cumple las normas internacionales de gestión de calidad, lo que garantiza una prestación de servicios fiable y coherente.
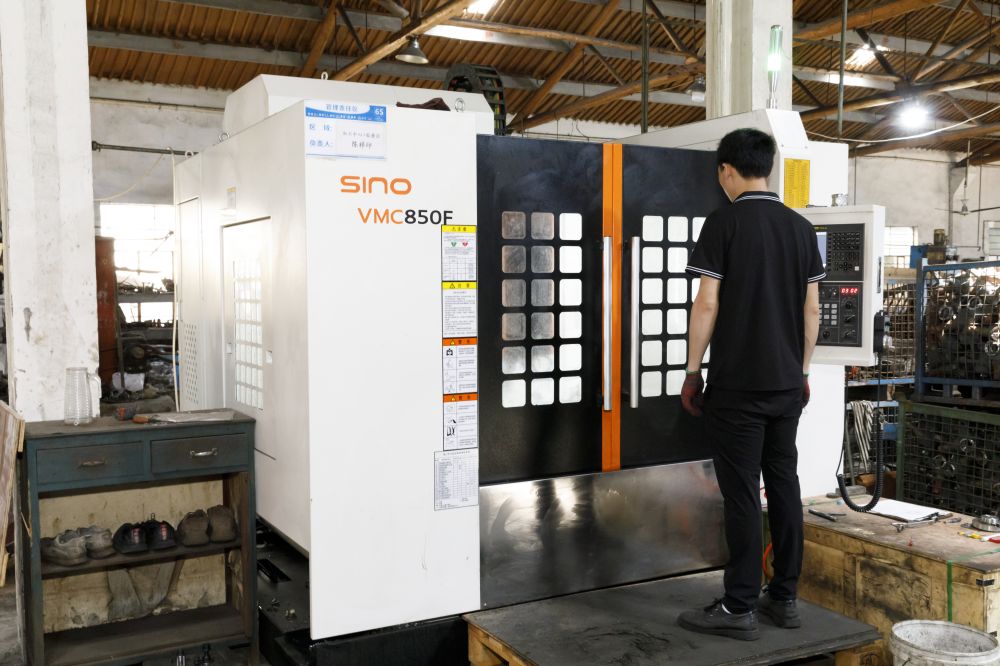
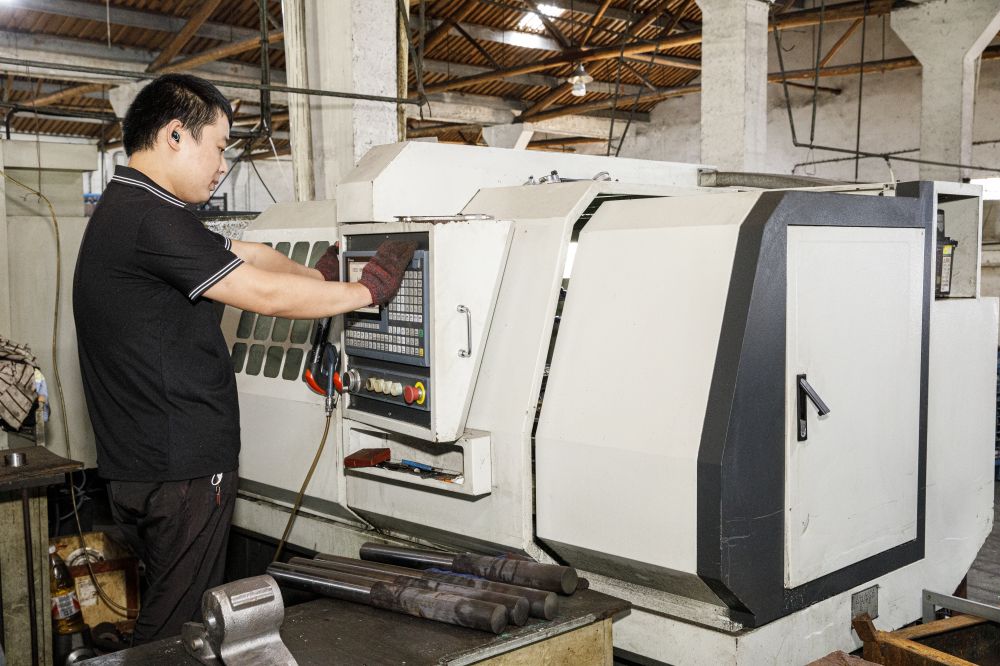
Piezas de torneado CNC de KEMING

Qué es el mecanizado por torneado CNC
El mecanizado de torneado CNC es un proceso de fabricación sustractivo en el que una pieza de trabajo, normalmente cilíndrica, gira contra una herramienta de corte para eliminar material y crear formas y características precisas. El proceso utiliza tornos CNC (control numérico por ordenador), que automatizan las operaciones de corte basándose en instrucciones programadas (código G). El torno hace girar la materia prima sujeta en un mandril, mientras que la herramienta de corte se mueve linealmente para dar forma a la pieza. Entre las operaciones habituales del torneado CNC se incluyen el refrentado, el roscado, el moleteado, el taladrado, el mandrinado, el escariado y el torneado cónico. Tras el mecanizado, la pieza acabada se separa del material en bruto para su posterior procesamiento, si es necesario.
Este proceso se utiliza ampliamente para producir piezas simétricas con gran precisión y repetibilidad. El torneado CNC puede manipular una gran variedad de materiales, incluidos metales como aluminio, acero, titanio y plásticos. Es ideal para fabricar componentes con geometrías cilíndricas, como ejes, casquillos, pasadores y piezas roscadas. El proceso ofrece tolerancias ajustadas, a menudo entre ±0,001″ y ±0,005″, lo que permite fabricar piezas que cumplen estrictos requisitos de calidad.
Operaciones de torneado CNC por KEMING
KEMING ofrece una amplia gama de servicios de torneado CNC que incluyen torneado recto, torneado cónico, moleteado, roscado, ranurado y tronzado. Empleamos herramientas de acero de alta velocidad y controlamos cuidadosamente los parámetros de corte, como la velocidad, el avance y la profundidad, para equilibrar la calidad y la eficiencia, garantizando que la precisión dimensional y el acabado superficial cumplan las especificaciones de diseño.
Giro recto
Esta operación utiliza herramientas de corte para reducir uniformemente el diámetro de una pieza giratoria, alcanzando un espesor predeterminado. Es ideal para eliminar rápidamente material con el fin de evitar variaciones de diámetro y suele utilizarse como paso de desbaste antes del acabado para obtener precisión dimensional.
Moleteado
KEMING ofrece operaciones de moleteado que crean patrones texturizados -como líneas dentadas, en ángulo o en intersección- en la superficie de la pieza de trabajo. Esto mejora el agarre al aumentar la fricción, por lo que es adecuado para componentes como pernos y tuercas. Para conseguir estos patrones se emplean herramientas de moleteado especiales.
Segmentación Separación
Esta técnica consiste en utilizar una herramienta de corte de un solo punto para cortar ranuras profundas en el material, separando eficazmente las piezas o eliminando secciones específicas de la pieza de trabajo original. Es esencial para producir componentes individuales a partir de una pieza mayor con precisión y exactitud.
Torneado cónico
La operación de torneado cónico de KEMING reduce gradualmente el diámetro de la pieza de trabajo de un extremo a otro inclinando cuidadosamente la herramienta de corte o la propia pieza. Este preciso proceso produce formas cónicas que se requieren habitualmente en diversas piezas de automoción y maquinaria.
Enhebrado
Realizamos el roscado desplazando cuidadosamente la herramienta de corte a lo largo de la pieza para cortar con precisión ranuras en espiral en su superficie externa. Este proceso crea roscas con un paso y una longitud específicos, esenciales para aplicaciones de fijación fiables en diversos conjuntos mecánicos.
Ranurado
Esta operación de mecanizado consiste en crear ranuras estrechas o anchas en la superficie de una pieza empleando herramientas de corte afiladas. Se utiliza específicamente para producir ranuras con anchuras y profundidades precisas, que son cruciales para diversas funciones mecánicas y requisitos de montaje.

Materiales de torneado CNC de KEMING
Keming, fabricante de piezas de torneado CNC con sede en China, trabaja con una gran variedad de materiales utilizados habitualmente en los procesos de torneado CNC. Sus materiales incluyen metales como aluminio, latón, acero inoxidable, acero, cobre, titanio y níquel, que se eligen por su resistencia, dureza y conductividad. Estos metales se aplican ampliamente en industrias como la aeroespacial, la de automoción y la de fabricación de maquinaria.
Además de metales, Keming también mecaniza plásticos y materiales compuestos como fibra de carbono y fibra de vidrio, apreciados por su ligereza, alta resistencia y rigidez. Los plásticos utilizados incluyen tipos con buena resistencia al desgaste y a la corrosión, adecuados para equipos electrónicos y de comunicación. Los materiales compuestos requieren herramientas especiales y control de parámetros para evitar daños durante el mecanizado.
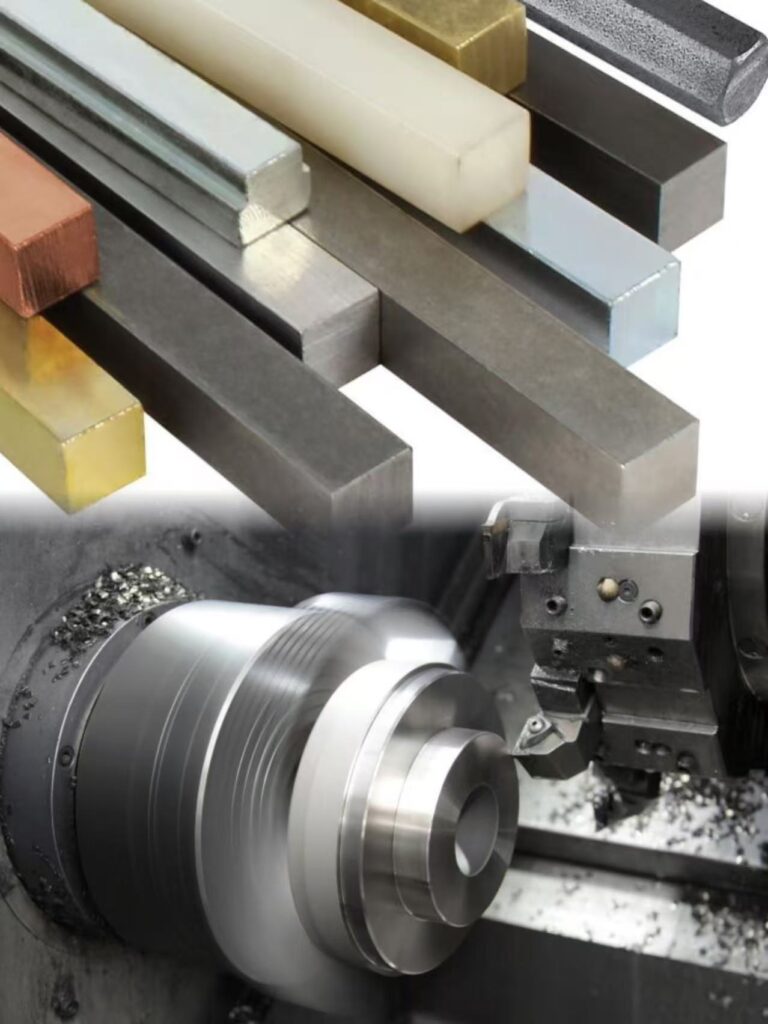
Metales para torneado CNC a medida
- Aluminio: Las aleaciones de aluminio (como 6061, 7075 y 5052) son las preferidas para el torneado CNC porque son ligeras, fuertes, resistentes a la corrosión y muy maleables. Permiten formas complejas y acabados suaves, por lo que son ideales para los sectores aeroespacial, automovilístico, médico, naval y electrónico.
- Aceros con bajo contenido en carbono: Las calidades como 1018 y los aceros de mecanizado libre como 12L14 son excelentes para el torneado CNC debido a su buena maquinabilidad, ductilidad y asequibilidad. Producen virutas manejables y suelen utilizarse para ejes, varillas, tornillos y pasadores en los que se requiere una resistencia moderada y facilidad de mecanizado.
- Aceros aleados: Los aceros aleados como el 4140 y el 4340 se seleccionan para piezas que requieren mayor resistencia, dureza o tenacidad. Esto se consigue a menudo mediante procesos especializados de tratamiento térmico. Con una mecanizabilidad moderada, los aceros aleados se utilizan ampliamente en la fabricación de piezas críticas como husillos, pernos y diversos componentes aeronáuticos.
- Aceros inoxidables: Las calidades de acero inoxidable más comunes, como 304, 316 y 17-4 PH, se utilizan por su excelente resistencia a la corrosión y su buena solidez. Tienen una maquinabilidad de buena a moderada y son adecuados para fabricar equipos de procesamiento de alimentos, componentes marinos, piezas de turbinas y diversos tipos de herramientas industriales.
- Cobre: El cobre se utiliza mucho por su excelente conductividad eléctrica y térmica. Además, su buena maleabilidad permite darle formas complejas con facilidad. Estas propiedades hacen del cobre un material ideal para contactos eléctricos, disipadores de calor, cableado y diversos componentes intrincados de la electrónica y la ingeniería.
El proceso de torneado CNC por KEMING
En KEMING, nuestro compromiso con la precisión, la calidad y el control de procesos garantiza que cada pieza torneada CNC cumpla o supere las expectativas del cliente. Nuestra experiencia en torneado CNC nos permite ofrecer componentes fiables y de alto rendimiento para una amplia gama de industrias. He aquí una introducción al proceso de torneado CNC de KEMING.

Confirme la geometría y el tamaño
Antes de iniciar cualquier operación de torneado, verificamos meticulosamente la geometría y las dimensiones de la pieza de trabajo comparándolas con los planos CAD proporcionados. Esto incluye la comprobación de detalles críticos como el diámetro, la longitud, los requisitos de acabado superficial, las tolerancias de mecanizado y otros parámetros esenciales para garantizar que la pieza de trabajo coincide con la intención del diseño.

Elija la herramienta de torneado adecuada
La selección de la herramienta de torneado adecuada es vital para el éxito del mecanizado. En KEMING, elegimos cuidadosamente las herramientas en función del material y la forma de la pieza de trabajo, teniendo en cuenta el diseño del filo de corte, los ángulos y la dureza de la herramienta. También ajustamos los parámetros clave del proceso, como la velocidad de rotación, el avance y la profundidad de corte, para optimizar el rendimiento y la vida útil de la herramienta.

Ajuste de los ejes de movimiento del torno
La calibración precisa de los ejes de movimiento del torno, incluidos el eje de avance longitudinal, el eje de avance transversal y el eje principal, se realiza antes del mecanizado. Este paso crucial garantiza que la herramienta de torneado se desplace con precisión por las trayectorias previstas, lo que permite realizar cortes de gran precisión y piezas acabadas con una calidad constante.
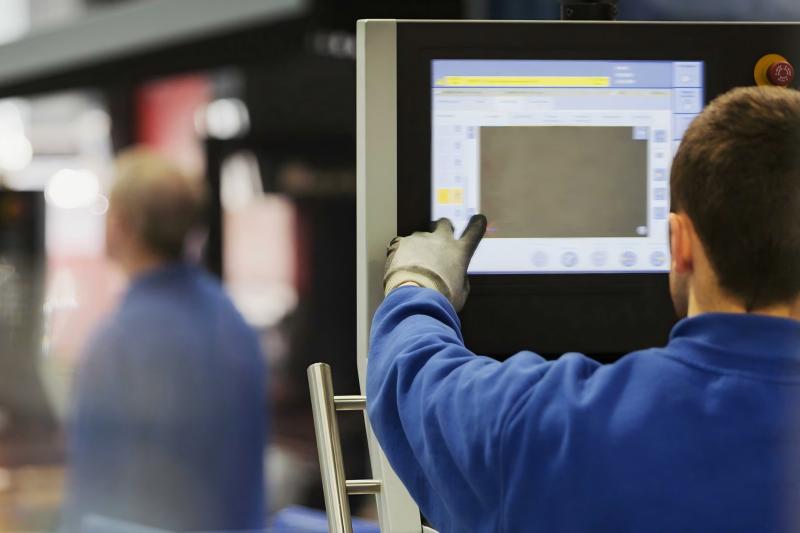
Parametrización del corte torneado
Predefinimos cuidadosamente los parámetros de corte esenciales, como la velocidad del husillo, el avance y la profundidad de corte, teniendo muy en cuenta el material específico de la pieza y los requisitos de mecanizado detallados. Esta configuración proactiva garantiza que el proceso de mecanizado se ajuste a los resultados deseados en términos de precisión, acabado superficial y eficiencia.
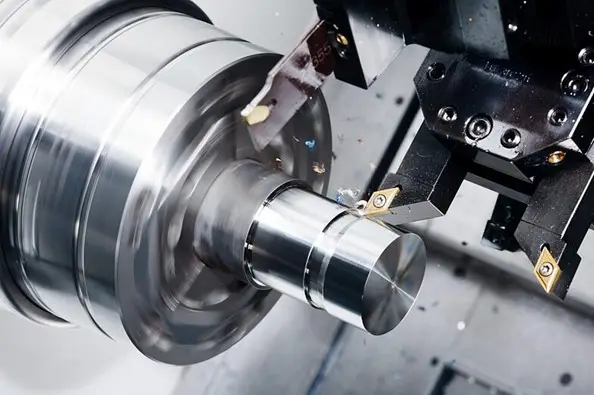
Mecanizado de torneado CNC
Durante el torneado, la herramienta se desplaza axial y transversalmente para cortar o rectificar. Mantener un espacio de contacto mínimo entre la herramienta de corte y la superficie de la pieza es absolutamente fundamental para lograr cortes precisos, suaves y exactos, al tiempo que se evita eficazmente cualquier daño potencial tanto a la herramienta como a la pieza durante el mecanizado.

Inspección y entrega
Tras el torneado, KEMING realiza inspecciones minuciosas de la pieza, comprobando las dimensiones, la forma, el acabado superficial y cualquier defecto. Para el torneado de ejes CNC, analizamos las especificaciones, utilizamos herramientas de acero de alta velocidad para comprobar la rugosidad de la superficie, ajustamos los parámetros de corte durante el mecanizado y verificamos la precisión final para garantizar que los productos cumplen estrictas normas de calidad.
Aplicaciones del torneado CNC de piezas
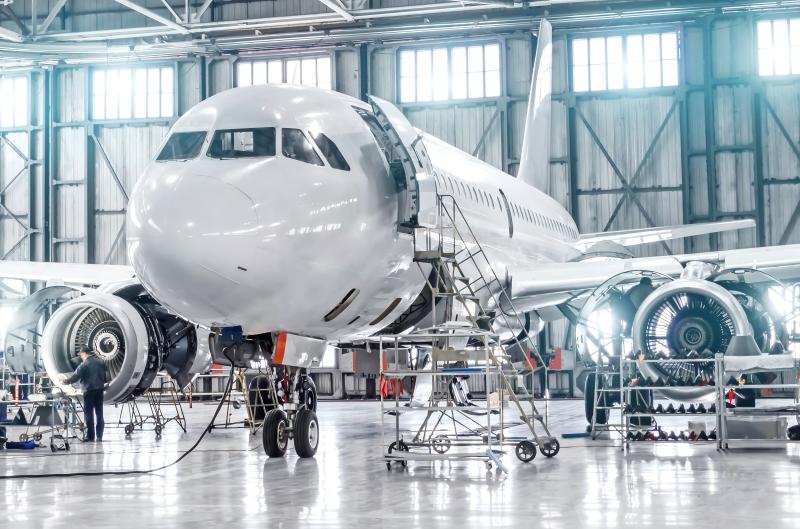
Aeroespacial
Fabricación de ejes, pasadores, espaciadores, casquillos, accesorios hidráulicos, pasadores de tren de aterrizaje y componentes de motor que requieren alta precisión y fiabilidad.
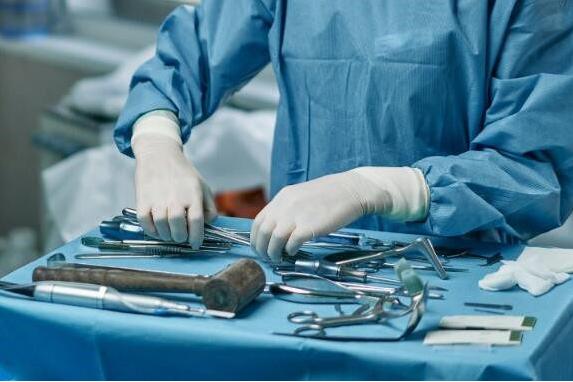
Médico
Creación de instrumentos quirúrgicos, implantes, tornillos óseos, implantes dentales y elementos de fijación con estrictos requisitos de calidad y biocompatibilidad.
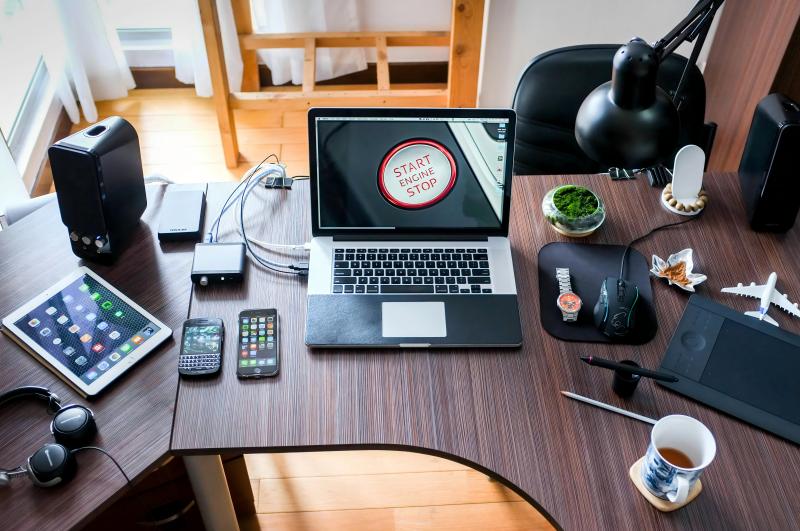
Electrónica
Producir conectores, terminales, clavijas de contacto y carcasas para dispositivos electrónicos, beneficiándose de la compatibilidad del torneado CNC con metales y plásticos.
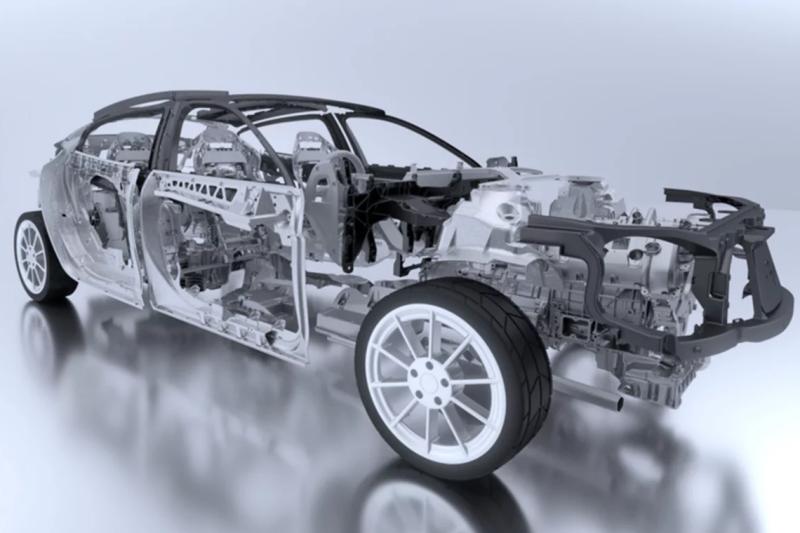
Automoción
Fabricación de ejes, árboles de transmisión, árboles de levas, cigüeñales, poleas, pernos y piezas de motor como bloques de cilindros y componentes del salpicadero, apoyando la fabricación a medida.
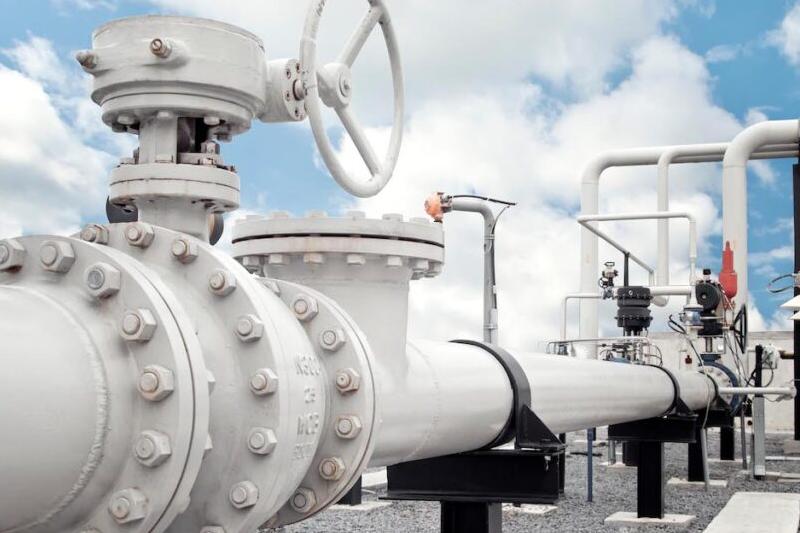
Petróleo y gas
Fabricación de válvulas, piezas de bombas, accesorios hidráulicos, acoplamientos y componentes de perforación esenciales para los sistemas de control y extracción de fluidos.
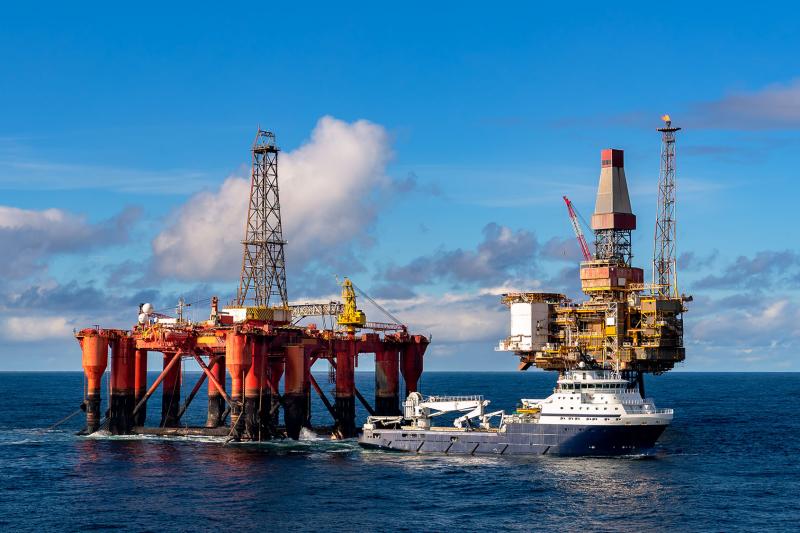
Marina
Mecanizado de torneado CNC de precisión de ejes de hélices, acoplamientos y componentes de motores marinos diseñados para soportar entornos oceánicos extremadamente duros.
Ponga sus piezas de torneado CNC en producción con KEMING hoy mismo
Toda la información y las cargas son seguras y confidenciales.