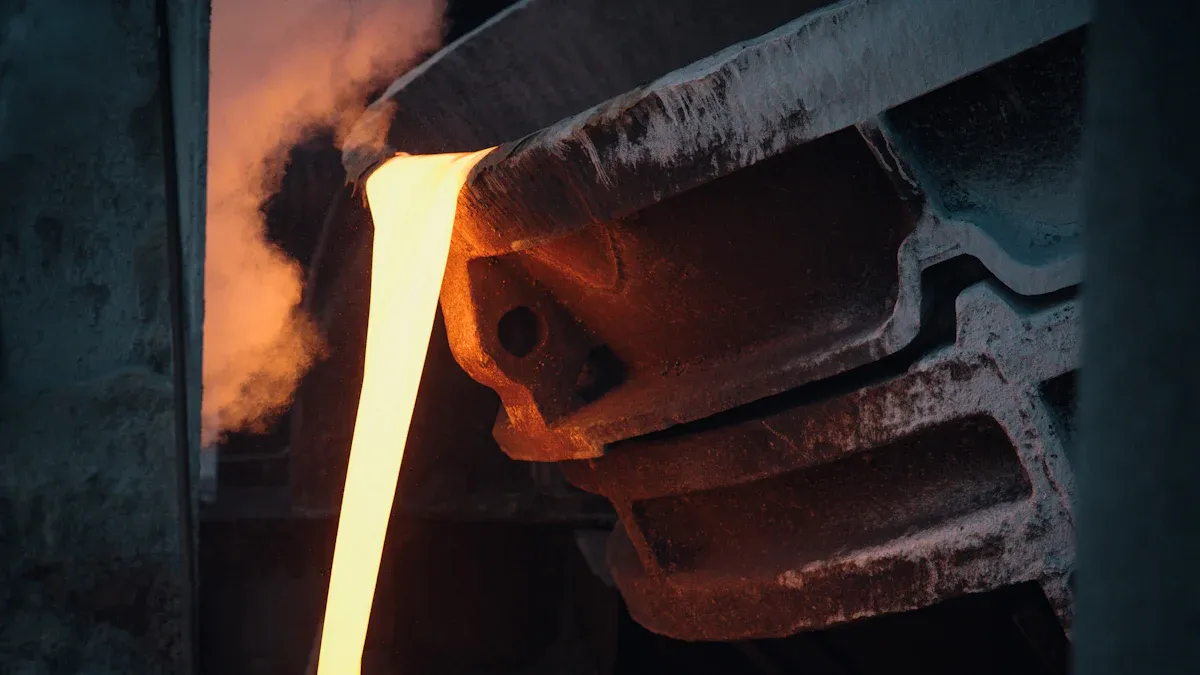
Investment casting and die casting are used for different applications. Investment casting is ideal for creating complex shapes and can be used with a wide variety of materials. Die casting, on the other hand, is known for its speed and high accuracy, making it suitable for producing large quantities of parts efficiently. When deciding between these processes, consider factors such as the material, the complexity of the part, and the required production volume. The table below highlights the differences between investment casting and die casting in terms of accuracy, cost, and speed:
Feature / Metric | Investment Casting | Die Casting |
---|---|---|
Dimensional Tolerance (up to 25mm) | ±0.250 mm | ±0.050 mm |
Minimum Wall Thickness | 1.00 mm | 0.50 mm |
Typical Production Rate | Up to 1000/hr | Up to 200/hr |
Minimum Production Quantity | 10 | 10,000 |
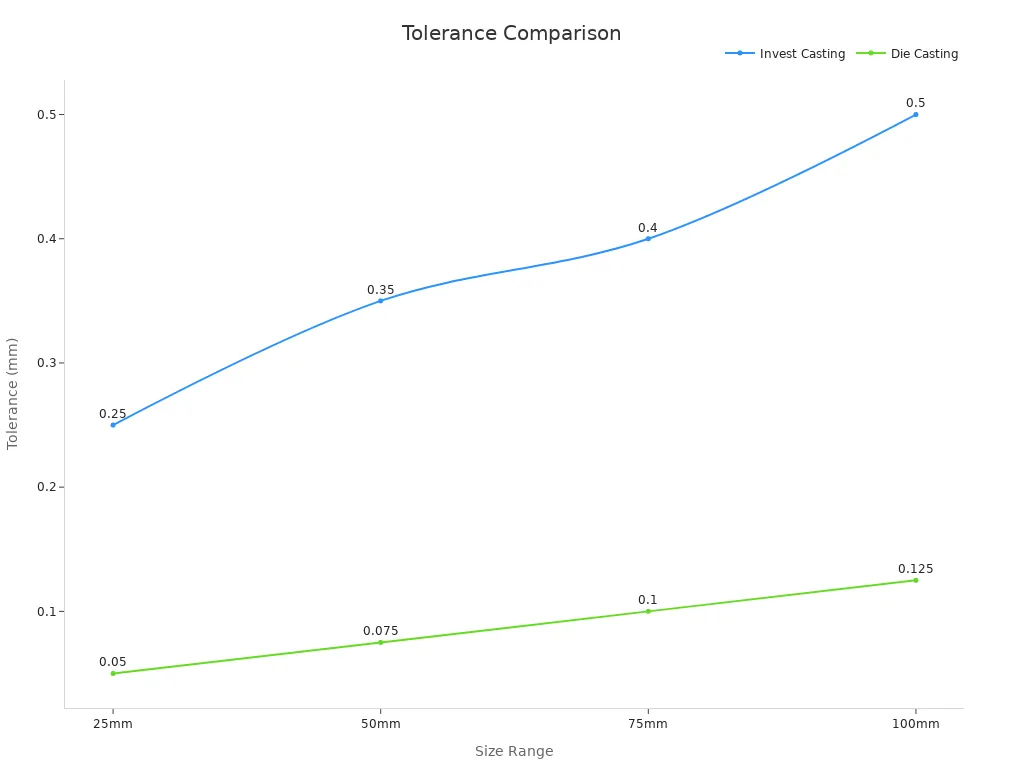
Consider the material, the shape, and the number of parts you need before selecting investment casting or another casting method.
Key Takeaways
- Investment casting works well for small or medium parts. It is good for parts with tricky shapes and tiny details. You can use many kinds of metals with it.
- Die casting is great for making lots of parts fast. It makes parts very exact. It mostly uses metals like aluminum and zinc.
- Pick investment casting if you need fewer parts. It is also good if you want to change the design or need lots of detail.
- Choose die casting if you need many parts made quickly. It is best when you care about speed, saving money, and exact sizes.
- Use the checklist to help pick the right casting method. Think about the shape, size, number of parts, and cost for your project.
Key Differences
Quick Comparison
You need to think about a few things when picking investment casting or die casting. Each one is good at something different. The table below shows how they are not the same:
Casting Process | Accuracy & Surface Finish | Dimensional Tolerances / Net Shape | Cost & Production Volume Suitability | Additional Notes |
---|---|---|---|---|
Sand Casting | Not as accurate; rougher surface | Shapes within about 1/4 inch | Cheaper; works for big parts | Good for heavy things like engine blocks |
Investment Casting | Very accurate; smooth surface | Very precise and can make hard shapes | Costs more; good for small to medium batches | Great for planes, medical, and power parts |
Die Casting | Very accurate; smooth surface | Close to final shape and size | Tools cost a lot; best for making many parts | Used for metals like aluminum; may need more work after |
Investment casting makes parts with lots of detail and smooth sides. It is good for tricky shapes and tight fits. Die casting also makes accurate parts but is faster and better for making lots of the same thing. Sand casting is not as exact and is best for really big parts.
What the part is made of matters too. For example, aluminum weighs less and melts at 660°C. Steel is heavier and melts at a higher temperature. These things change which casting method you should use.
Tip: How smooth a part is can change how long it lasts. Smoother parts from investment casting or die casting can help them last longer and not wear out as fast.
When to Use Each
Picking the right casting way depends on what you need. Here are some tips:
- Pick investment casting if:
- The part is tricky or has small details.
- You want a very smooth finish.
- You only need a small or medium number of parts.
- The material is hard to cast with other ways.
- Pick die casting if:
- You need thousands or millions of the same part.
- The part is not too tricky.
- You use a metal like aluminum or zinc.
- You need to make parts quickly.
- Sand casting is best for really big parts or if you want to save money.
Each way is good for something. Investment casting is best for tricky shapes and being flexible. Die casting is best for making lots of parts fast and saving money.
Investment Casting Process
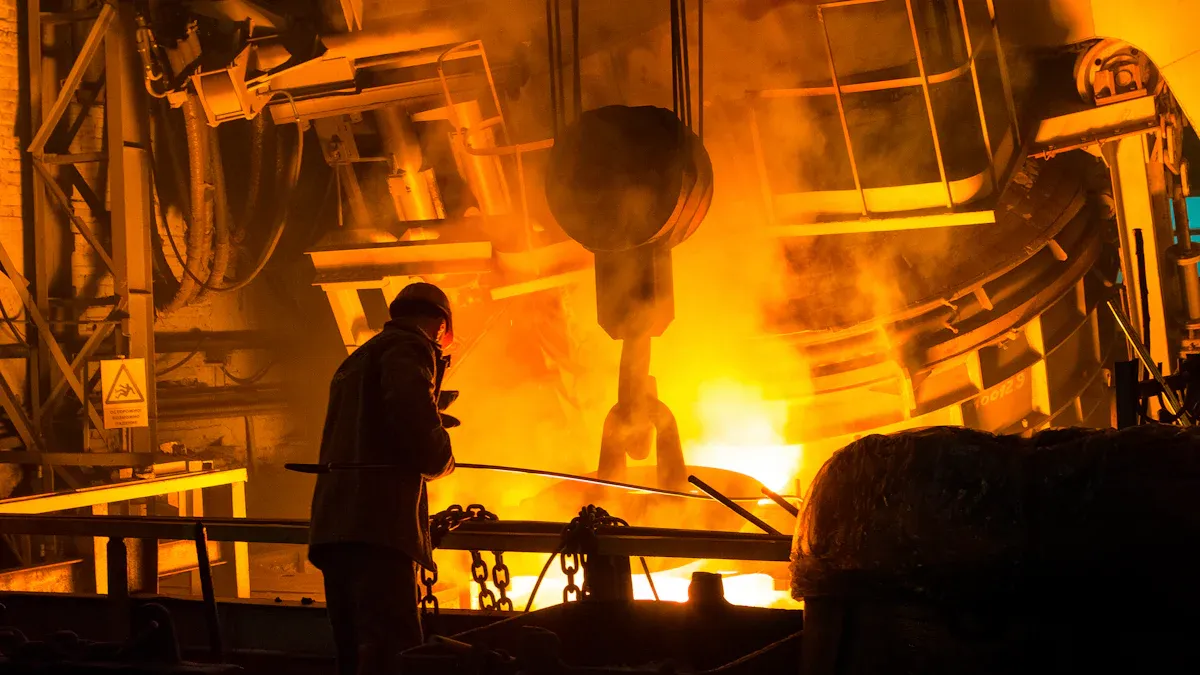
How It Works
Investment casting makes metal parts in many steps. First, workers make a wax pattern that looks like the part. They dip the wax in a ceramic liquid. Then, they cover it with fine sand. This step is done many times to make a hard shell. When the shell dries, they heat it up. The wax melts and leaves a hollow space inside the shell. Next, hot metal is poured into the shell. The metal fills every small space and copies all the details. When the metal cools, workers break the shell off. The metal part looks just like the wax pattern. This way, you can make parts with tricky shapes and tiny details.
Note: Wax 3D printing can make patterns faster and more exact. This helps stop mistakes from happening.
Strengths and Limits
Investment casting has many good points for making exact parts:
- It can make parts very close to the right size, even as close as ±0.05 mm.
- You can use many metals, like stainless steel, aluminum, and titanium.
- The parts come out smooth and can have hard shapes.
- Special machines check if each part is the right size.
- Hot isostatic pressing (HIP) can get rid of tiny holes. This makes the parts stronger and better.
- You do not need to do a lot of extra cutting or shaping. This saves time and money.
- It works well if you only need a few or some parts.
But, investment casting is not always the best way. It takes a while because each mold is made by hand. It is best for parts that need lots of detail or special metals. If you need a lot of parts fast, another way might be better.
Die Casting Process
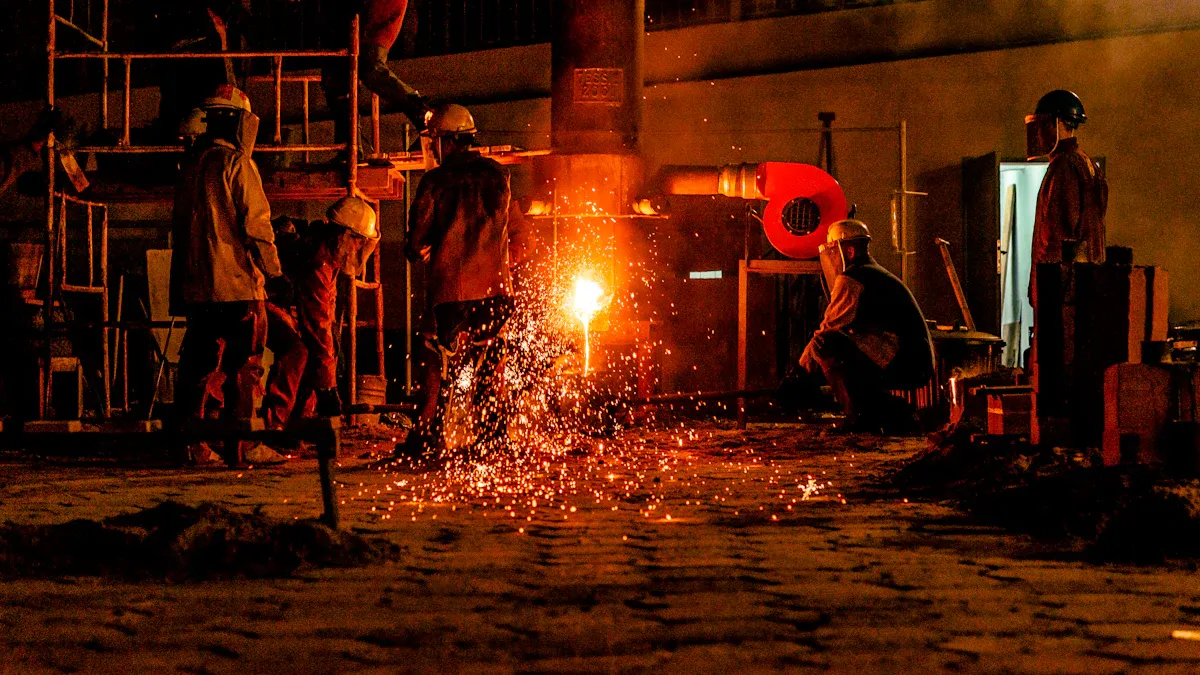
How It Works
Die casting uses strong pressure to push melted metal into a steel mold called a die. First, workers melt metals like aluminum or zinc in a hot oven. They pour the melted metal into a special chamber. A plunger quickly pushes the metal into the die. The metal fills every space inside the mold. The die cools the metal fast, so the part gets hard quickly. Workers open the die and take out the finished part. This way, factories can make thousands of parts that all look the same.
Die casting works best with metals that melt at lower temperatures. The dies can have many shapes and small details. Factories use machines to run the process. This helps make parts faster and with fewer mistakes.
Note: Die casting can make thin walls and sharp corners that are hard to do with other ways.
Strengths and Limits
Die casting has many good points for making metal parts:
- High speed: Machines can make lots of parts every hour.
- Great accuracy: Parts come out with tight fits and smooth sides.
- Cost savings: Making many parts lowers the price for each one.
- Less waste: The process uses just enough metal, so there is not much left over.
- Good for automation: Factories use robots and belts to move parts and keep them good.
A real example shows how changes can make die casting better:
Metric | Initial State | Improvement Achieved |
---|---|---|
Lot size | 60,000 pcs/year | N/A |
Closing force | 1600 tons | Reduced to 1200 tons |
Shot weight | 2885 grams | Reduced to 2470 grams (14% reduction) |
Cycle time | 26.5 seconds | 10% reduction |
Volume porosity | High | 62% reduction |
Revenue | ~€38,000 | ~€100,000 (165% increase) |
Output | Baseline | +7 pcs/hour |
Quality | Baseline | 50% improvement |
Studies show that using vacuum systems in die casting can cut gas bubbles in aluminum parts from 4% to 1%. This makes parts stronger and lets factories use more spaces in each die. This helps make parts faster and saves money.
- Companies use FIFO systems to track parts and make them better.
- Conveyors link machines, saving time and stopping mistakes.
- Good equipment keeps the process running almost all week.
- Lean manufacturing helps control costs and get better results.
Die casting is best for making lots of parts, simple or medium shapes, and metals like aluminum or zinc. It may not work well for very big or thick parts. Factories pick die casting when they need many parts fast, with good quality and low cost for each one.
Materials and Compatibility
Investment Casting Materials
Investment casting works with many kinds of metals. It can use both ferrous and non-ferrous alloys. Stainless steel, carbon steel, aluminum, and copper alloys are used a lot. Factories pick investment casting for parts with thin walls or lots of details. Cu-Sn alloys, which are copper and tin, are good for making thin and exact parts. The process needs the metal to flow well into the mold. This is called fluidity. Fluidity means how easy the metal moves in the mold. If there is more tin in the alloy, the metal does not flow as well. This can make mistakes in the part. Pouring the metal hotter and using less tin helps it flow better and stops problems.
Note: Investment casting makes smooth parts and can create shapes that other ways cannot.
Alloy/Process | Key Compatibility Factors | Challenges/Advantages |
---|---|---|
Cu-Sn (Copper-Tin) | Thin walls, precise shapes | High tin lowers fluidity, more defects; higher temp and less tin help |
AA7075 – Investment Casting | Low cooling rate, good surface finish | Can cause coarse phases, hot cracks, shrinkages; high precision possible |
Die Casting Materials
Die casting uses metals that melt at lower heat. Aluminum, zinc, and magnesium are the most used. These metals fill the die fast and cool quickly. Factories use die casting when they need to make many parts. Some alloys, like AA7075, do not work well in die casting. This alloy needs to cool very fast, which can cause problems. Thin-wall die casting with AA7075 does not work because the metal does not flow well. Most die casting metals must move easily and get hard without cracks or holes.
- Aluminum alloys: Used for car parts and electronics.
- Zinc alloys: Good for small, detailed parts.
- Magnesium alloys: Chosen for lightweight parts.
Alloy/Process | Key Compatibility Factors | Challenges/Advantages |
---|---|---|
AA7075 – Die Casting | High cooling rate needed | Causes defects; thin-wall casting not successful; fluidity issues present |
Aluminum, Zinc, Mg | Good fluidity, fast cooling | Best for high volume, simple to medium shapes |
Tip: Pick the right metal by thinking about the part’s shape, size, and how many you need.
Part Complexity
Design Flexibility
Design flexibility is important when picking a casting process. Investment casting lets engineers make parts with tricky shapes and thin walls. This process uses wax patterns, so almost any shape can be made. Designers can add holes, curves, and small features easily. Die casting is also flexible, but it works best for simple shapes. It is better for parts with even wall thickness. Sharp corners and deep undercuts are hard to do with die casting.
A new study shows how new designs can help casting. Engineers used 3D sand-printing to make special sprue shapes. These shapes helped metal flow better and lowered mistakes. The table below shows what happened:
Metric | Result for Novel Sprue Designs (3D Sand-Printing) | Comparison to Traditional Gating |
---|---|---|
Reduction in overall casting defects | Up to 99.5% reduction (conical-helix sprue) | Significant defect reduction |
Reduction in inclusions | 35% reduction (conical-helix sprue) | Lower inclusions confirmed by SEM |
Mechanical strength improvement | 8.4% increase in ultimate flexural strength | Improved mechanical performance |
Note: Special gating systems, made with new design tools, can make cast parts stronger and cleaner.
Detail and Precision
Detail and precision are important for parts that must fit or move well. Investment casting is great at showing tiny details and sharp edges. The process copies the wax pattern exactly. Even small logos or words can show up on the final part. Die casting also makes accurate parts, but it may not show as much detail as investment casting. Both ways make smooth surfaces, but investment casting often shows more detail.
Designers should think about how much detail their part needs. If a part needs small grooves, tiny holes, or tricky curves, investment casting is best. Die casting is good for parts that need to be precise but have simple shapes.
Size and Weight
Small vs Large Parts
Part size plays a big role in choosing the right casting process. Investment casting works best for small to medium parts. This method can create pieces as light as a few grams and up to about 100 kilograms. Die casting handles small to medium parts as well, but it can also make parts up to 300 kilograms. Factories often use die casting for items like automotive housings or electronic enclosures, which need to be both light and strong.
Sand casting and centrifugal casting are better for very large or heavy parts. These methods can handle pieces that weigh several tons. When engineers need a part with fine detail and a smooth finish, they often pick investment casting for smaller items. Die casting is chosen when many medium-sized parts are needed quickly.
Tip: For tiny, detailed parts, investment casting offers the best results. For bigger, bulkier parts, sand casting or centrifugal casting may be more practical.
Weight Factors
Weight affects not only the casting method but also the cost and speed of production. Lighter parts are easier to handle and cool faster, which helps increase production rates. Heavier parts take longer to cool and may need special handling equipment.
The table below shows how different casting methods match up with part weight and other factors:
Casting Method | Typical Weight Range (kg) | Shape Capability | Cost Level | Production Rate | Tolerance (mm) | Notes on Suitability |
---|---|---|---|---|---|---|
Sand Casting | 0.05 to unlimited | All shapes | Low to medium | Low (<100/hr) | ±1.0 | Good for very large or heavy parts |
Investment Casting | 0.005 to 100 | All shapes | High | Medium to high (up to 1000/hr) | ±0.05 | Best for small to medium parts with fine detail |
Die Casting | 0.05 to 300 | Most shapes | Low to medium | High (5–200/hr) | ±0.05 | Great for medium weight parts, high production rates |
As the table shows, investment casting and die casting both suit small to medium parts, but die casting can handle heavier pieces. Sand casting is the top choice for the largest and heaviest parts. Weight and size guide engineers to the most efficient and cost-effective casting method.
Production Volume
Low and Medium Runs
Investment casting works well for low and medium production runs. Companies often choose this process when they need between 10 and a few thousand parts. The setup for investment casting does not require expensive tooling. This makes it a smart choice for custom parts or when testing new designs. Engineers can change the design without high extra costs.
Investment casting also allows for quick changes. If a company needs to adjust a part, they can do so by making a new wax pattern. This flexibility helps when making prototypes or small batches. Many industries, such as aerospace and medical, use investment casting for these reasons.
Tip: Investment casting is ideal for projects that need high detail but do not require mass production.
High-Volume Runs
Die casting shines in high-volume production. Factories use this method when they need thousands or even millions of parts. The process uses strong steel dies that last for many cycles. Although the initial cost for the die is high, the cost per part drops as more parts are made.
Die casting machines can produce parts quickly. This speed helps companies meet large orders on time. Automotive and electronics industries often use die casting for this reason. The process works best for parts that do not change often.
Production Volume | Investment Casting | Die Casting |
---|---|---|
Low (10–1,000) | ✅ Best Choice | ❌ Not Efficient |
Medium (1,000–10,000) | ✅ Good Option | ✅ Good Option |
High (10,000+) | ❌ Costly | ✅ Best Choice |
Note: For high-volume runs, die casting offers the lowest cost per part and the fastest production rates.
Tolerances and Finish
Precision Levels
Tolerances tell us how close a part is to its planned size. Both investment casting and die casting can make parts with tight tolerances. Die casting usually makes parts with even better precision. For example, die casting can make small features with tolerances as tight as ±0.05 mm. Investment casting usually keeps tolerances around ±0.25 mm. Sometimes, with careful work, investment casting can do even better for some parts.
Data from high-precision castings show that 99.73% of hole sizes stay within ±3 standard deviations. This means most parts meet strict quality rules. When the temperature changes during casting, parts can get bigger or smaller. If the temperature goes up by 1°C, the size may change by about 8.5 micrometers. Engineers use special steps to fix these changes and keep parts accurate.
Using good measurement tools and steady processes helps factories make sure parts fit and work right.
Surface Quality
Surface finish means how smooth or rough a part feels and looks. Both investment casting and die casting make smooth surfaces. Investment casting often shows more tiny details. Inspectors use standards like ANSI/ASME B46.1 to check surface finish. They take many measurements and find the average, because one reading might not show the real texture.
- Surface finish has lay, waviness, and roughness.
- RMS and Ra are two ways to measure roughness. RMS numbers are usually about 11% higher than Ra for most surfaces.
- Factories can make surfaces smoother by changing the finishing media or how they hold the part.
It is important to pick the right way to measure. Contact profilometers, non-contact optical tools, and looking at the part all help check the surface. Picking the wrong place or using the wrong unit can cause mistakes and slow things down.
Tip: Always say where and how to measure surface finish. This helps avoid mistakes and keeps production moving.
Speed and Lead Time
Production Speed
Production speed plays a big role in choosing a casting process. Die casting stands out for its fast cycle times. Factories using hot chamber die casting can make between 150 and 2,000 parts per hour, depending on the size of the component. This high speed makes die casting a top choice for large orders. Cold chamber die casting works a bit slower but still supports high-volume production.
Investment casting takes more time. Workers must create wax patterns, build ceramic shells, and wait for each layer to dry. Each step adds to the total time needed. As a result, investment casting usually produces fewer parts per hour than die casting. This process fits best for projects that need high detail but not huge quantities.
The table below shows how production speed compares for different casting methods:
Casting Process | Production Volume Suitability | Cycle Rate (Parts/Hour) | Notes on Speed and Efficiency |
---|---|---|---|
Hot Chamber Die Casting | High (≥10,000 pieces) | 150–2,000+ | Fastest, best for mass production |
Cold Chamber Die Casting | High (≥10,000 pieces) | Slower than hot chamber | Good for certain alloys, still high speed |
Investment Casting | Low to medium | Not specified, slower than die | Best for detail, not for speed |
Sand Casting | Low (up to 500 pieces) | Slowest | Used for large, heavy parts, not for speed |
Die casting offers the fastest production rates, making it ideal for industries that need many identical parts quickly.
Setup Time
Setup time means how long it takes to get ready for production. Die casting needs special steel dies. Making these dies takes time and skill. Once the dies are ready, the process runs quickly. This setup works well for long runs because the cost and time spread over many parts.
Investment casting has a different setup. Workers make wax patterns and ceramic molds for each batch. The setup time is shorter than die casting, especially for small runs. This makes investment casting a good choice for prototypes or custom parts.
Production lead time includes every step from start to finish. Factories look at each stage to find delays and improve speed. Die casting usually has a longer setup but much faster production. Investment casting has a shorter setup but slower part-making.
Tip: For fast delivery of large orders, die casting is the best option. For flexible, small-batch production, investment casting saves time in setup.
Cost Factors
Tooling Costs
Tooling costs play a big role in choosing between investment casting and die casting. Investment casting needs special molds for each part. These molds take time and skill to make. The cost for tooling in investment casting is high, especially for complex shapes. However, the process allows for changes if the design is not final. This flexibility helps when making prototypes or custom parts.
Die casting requires a large upfront investment for tooling. The steel dies used in this process can cost around $45,000. Making these dies takes about 12 weeks. Changing the die after production starts is hard and expensive. Because of this, die casting works best for designs that will not change. Companies often choose die casting when they plan to make many parts and feel sure about the design.
Casting Method | Tooling Cost Characteristics | Production Volume Suitability |
---|---|---|
Investment Casting | Higher initial tooling costs; complex molds | Low to medium volumes |
Die Casting | High upfront tooling cost (e.g., ~$45,000) | High volumes |
Tip: For new or changing designs, investment casting offers more flexibility. For stable, high-volume projects, die casting tooling pays off over time.
Per-Part Costs
Per-part costs depend on how many parts a company needs. Investment casting has moderate per-part costs. For example, a part may cost about $100 to make. This price stays steady for small or medium runs. The cost does not drop much as volume increases.
Die casting shines when making many parts. The per-part cost can be as low as $30. This low price comes after the company makes enough parts to cover the high tooling cost. The break-even point is about 850 parts. After this, die casting becomes the cheaper choice.
- Investment casting suits small batches or custom orders.
- Die casting is best for large orders with mature designs.
Companies should think about how many parts they need and how often the design might change. This helps them pick the most cost-effective casting method.
Choosing the Right Process
Decision Checklist
Picking the best casting process can be hard. Designers and engineers use special tools to help them choose. These tools compare what the project needs with what each casting method can do. They look at things like what material is used, the shape and size of the part, how much it costs, and how many parts are needed. Some tools have big lists of facts about each process. Others use points to see which process is the best match.
Here is a checklist to help you find the right casting process for your project:
Project Requirement | Die Casting | Investment Casting | Sand Casting |
---|---|---|---|
High production volume | ✅ Best fit | ❌ Not ideal | ❌ Not ideal |
Complex shapes | ⚠️ Some limits | ✅ Best fit | ⚠️ Some limits |
Tight tolerances | ✅ Excellent | ✅ Very good | ❌ Less precise |
Smooth surface finish | ✅ Excellent | ✅ Excellent | ❌ Rougher |
Low to medium volume | ❌ Costly | ✅ Best fit | ✅ Good fit |
Large part size | ⚠️ Some limits | ⚠️ Up to medium size | ✅ Best fit |
Fast lead time | ✅ Fastest | ⚠️ Moderate | ❌ Slow |
Low tooling cost | ❌ High | ⚠️ Moderate | ✅ Low |
Design changes needed | ❌ Difficult | ✅ Flexible | ✅ Flexible |
Wide material choice | ⚠️ Limited | ✅ Wide range | ✅ Wide range |
Tip: Use this table to help you decide. Think about which needs are most important for your project.
How Experts Make the Choice
- Designers use computer systems with lots of facts about each casting method. These systems help pick the best option based on what the part needs.
- Some methods give each process a score for things like how close the size is, how smooth the part is, and how many parts you need.
- Some tools use fuzzy logic to help with things that are hard to measure, like how smooth a part feels or how tricky the shape is.
- Cost models help compare all the costs, like making the mold, paying workers, and finishing the part.
- Some systems mix numbers and expert ideas to help make the final choice.
- Newer ways use both scoring and fuzzy logic to rank old and new casting methods.
Real-World Examples
- A pump company made a big, tricky part in just four weeks by using 3D-printed patterns and investment casting. This gave them the speed and accuracy they wanted.
- Engineers got smoother parts by switching to fast casting with 3D-printed patterns. They saved time and did not need new molds.
- A team fixed leaks in pump parts by using computer simulations. They found the problem fast and made the parts better.
- One company put many pieces into one casting. This made the part stronger and saved money.
Note: Many projects use expert advice, computer tools, and real tests to pick the best casting process.
Steps to Decide
- Write down what matters most for your project, like shape, size, number of parts, and finish.
- Look at the table above to see which casting method fits your needs.
- Use decision tools or ask an expert if your project is tricky.
- Check case studies or old projects that are like yours.
- Pick the process that matches your goals the best.
Remember: The best process depends on what you need. Take your time to compare choices and ask experts if you are not sure.
Investment casting is good for parts with tricky shapes and lots of detail. It also works with many different materials. Die casting is better when you need to make many parts fast and they must be very exact. You can look at the decision table to help you choose what you need. Experts say it is smart to check quality using X-rays and strength tests for both ways. If your part is special or hard to make, a casting expert can help you pick the best way and watch over things like how the mold is made and how fast it cools.
FAQ
What is the main difference between investment casting and die casting?
Investment casting uses wax and ceramic molds to make detailed parts. Die casting uses metal molds and strong pressure to make lots of parts fast. Each way is good for different jobs.
Which casting method works best for small production runs?
Investment casting is good for small or medium batches. It does not need costly tools. Companies can change the design if needed. Die casting is better for making many parts at once.
Can both methods use the same metals?
No, they cannot. Investment casting works with many metals like steel and titanium. Die casting mostly uses aluminum, zinc, or magnesium. The metal you pick depends on the process.
How do tolerances compare between the two methods?
Die casting makes parts with tighter tolerances, as close as ±0.05 mm. Investment casting is also precise but usually stays around ±0.25 mm.
Which process gives a smoother surface finish?
Both ways make smooth parts. Investment casting often shows more tiny details and fine texture. Die casting also makes smooth parts, especially when making many at once.