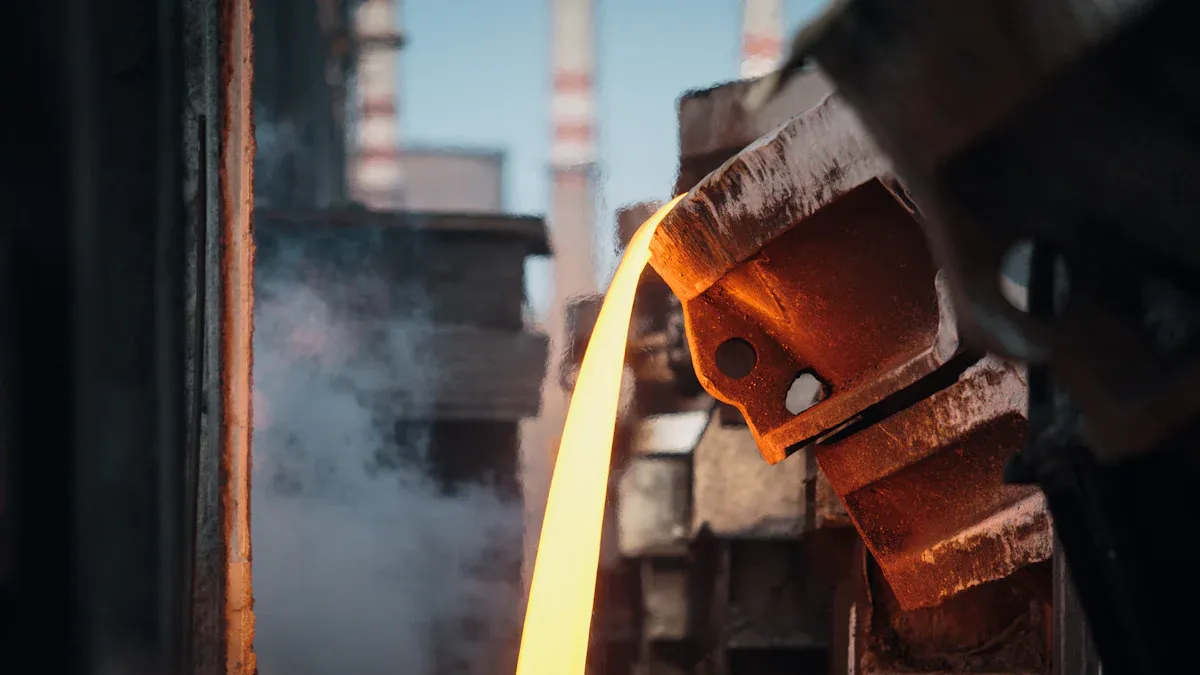
Many engineers and makers see that sand casting produces parts that are not as precise as those made by other methods. Studies show that traditional sand casting can be up to 31.6% less accurate than newer techniques like ablation sand casting. Dimensional accuracy is crucial because small variations in sand, binder, or how tightly the sand is packed during sand casting can cause parts to warp or have defects. In industries such as aerospace and automotive, closely monitoring these factors in sand casting helps ensure parts meet strict quality standards.
Key Takeaways
- Picking the right sand and watching moisture and compaction keeps molds strong. This helps parts keep their correct size.
- Good pattern design and checking often stop size mistakes. This also cuts down on waste in sand casting.
- Controlling how hot the metal is, putting molds together right, and careful handling help parts cool evenly. This keeps them close to the planned size.
- Placing cores exactly and supporting them well stops inside shape problems. This helps parts stay accurate.
- Checking parts often with tools like 3D scanners and using best methods finds problems early. This makes the final part better.
Main Factors in Sand Casting
Dimensional accuracy in sand casting depends on a few main things. Every step in sand casting can change the part’s size and shape. Knowing these things helps engineers and makers control tolerance and make better parts. The next sections talk about the main things that affect how close the part is to the right size in custom sand casting.
Sand and Mold Properties
Sand and mold materials are very important in sand casting. Different kinds of sand, like new or reclaimed sand, change how well the mold keeps its shape. Reclaimed sand usually keeps its shape better because it does not change much with heat. The size and shape of sand grains, plus how much binder and water there is, change how the sand packs and how strong the mold is. Things like potash or alkali feldspars can make the sand grains stick together less, which can cause problems or bad tolerance. The sand’s strength, especially how well it bends, helps the mold stay safe when moved or filled. Good gas flow and easy breaking of the mold help stop problems and make it easier to take out the core after casting. Controlling these sand casting materials is needed to meet tight tolerance.
Note: Tests show that reclaimed sand cores break apart more easily and do not grow much with heat, which helps make parts closer to the right size.
Pattern Design
Pattern design changes both the cost and how close the part is to the right size. Patterns with lots of cores or small details can cause more changes in size. Studies show that more cores and harder shapes make the tools and making the part cost more. This also means there is a bigger chance for mistakes and waste. For example, in train air brake and turbocharger parts, adding more cores or changing their shape made costs and mistakes go up. Custom sand casting often needs special patterns, so careful design helps keep parts close to the right size and cuts down on waste.
Process Control
The sand casting process has many steps where small changes matter. Pouring temperature, pouring speed, and how the mold is filled all change the final part. If the temperature is too high or low, the metal may shrink or grow in ways you do not want, making the part the wrong size. Water in the sand and how the sand is packed also matter. Studies using math found that pouring temperature and sand mix have a big effect on strength, hardness, and surface look. Keeping the sand casting process steady helps make sure every part is the same.
Mold Assembly
Mold assembly means putting together the mold and any cores needed. Lining up the mold parts is very important in custom sand casting, especially when you need tight tolerance. If the mold halves or cores move during assembly, the part can have problems or be the wrong size. The kind of sand casting mold, like if it uses CO2, cement, or natural binders, also changes how well the mold stays together when pouring. Good assembly helps stop the mold from moving and makes the part closer to the right size.
Post-Casting Steps
After the metal cools and gets hard, steps like taking the part out, cleaning, and machining can change the size. Rough handling or shaking when removing the part can bend or twist it. Machining and finishing must think about the first tolerance from sand casting. Checking with calipers or 3D scanning helps see if the part is the right size. Custom sand casting often needs extra care in these steps to make sure the part matches the plan.
Main Factor | Key Influence on Tolerance and Dimensional Accuracy |
---|---|
Sand and Mold Properties | Sand type, grain size, binder, and impurities affect mold stability and accuracy |
Pattern Design | Complexity, number of cores, and geometry impact variation and cost |
Process Control | Pouring temperature, sand mix, and handling influence final size |
Mold Assembly | Alignment and mold type affect risk of shift and defects |
Post-Casting Steps | Removal, cleaning, and machining can alter final dimensions |
Tip: Watching each of these main things closely helps makers get better tolerance and higher quality in sand casting.
Dimensional Accuracy Challenges
Sand Casting vs. Other Methods
Different casting methods give different levels of accuracy. Sand casting usually makes parts with rougher surfaces and less exact shapes. This is because the sand mold can move or break during casting. Other methods, like die casting and investment casting, use stronger molds. They also use more controlled settings. These methods make parts with smoother surfaces and tighter size limits.
The table below shows how smooth the surfaces are for each casting process. Lower RMS numbers mean smoother surfaces and better accuracy.
Casting Process | RMS Surface Finish Range (µin) |
---|---|
Die Casting | 20 – 120 |
Investment Casting | 60 – 200 |
Shell Mold Casting | 120 – 300 |
Centrifugal – Standard Tooling | 400 – 500 |
Centrifugal – Permanent Mold | 20 – 300 |
Static – Permanent Mold | 200 – 420 |
Normal Non-Ferrous Sand | 300 – 560 |
Normal Ferrous Green Sand | 560 – 900 |
Die casting and investment casting make much smoother parts than sand casting. Green sand molds, used in sand casting, often make the roughest surfaces. Rough surfaces make it hard to keep parts the right size. Many sand cast parts need extra work to meet strict rules.
Note: Resin-bonded sand molds can make parts more accurate, but they cost more than green sand molds.
Sources of Variation
Many things can change the final size and shape of cast parts. The sand mold can change shape when hot metal is poured in. Water in the sand, how the sand is packed, and the metal’s heat all matter. Even small changes in these steps can make parts too big, too small, or bent.
Pattern wear is another problem. Over time, the pattern used to make the mold can lose its shape. This makes the molds less accurate and causes more changes in the finished parts. Moving or handling the mold before the metal gets hard can also cause shifts or mistakes.
Careful control of each step helps stop these problems. Regular checks and good worker training help keep parts close to the right size.
Sand and Mold Material
Sand Type and Quality
Sand type and quality play a big role in how close a cast part comes to its planned size. Different sands, such as silica or chromite, have unique grain shapes and sizes. These features affect how well the sand holds together and how smooth the final part looks. High-quality sand casting materials help molds keep their shape during pouring and cooling. Poor sand can lead to rough surfaces or even cracks in the mold.
Quality checks help makers choose the right sand casting materials. They use several tests and tools to measure how well the sand works:
- Workers measure cast parts with calipers, micrometers, or coordinate measuring machines to check if the size matches the plan.
- They use hardness and tensile tests to see if the part is strong enough.
- Non-destructive tests, like X-rays, help find hidden problems inside the part.
Good sand casting materials also help control shrinkage and stop defects from forming. Makers often run chemical tests to make sure the sand does not add unwanted elements to the metal.
Compaction and Moisture
Compaction means pressing the sand tightly around the pattern. If the sand is too loose, the mold may break or shift. If it is too tight, the sand can crack when the hot metal is poured. Moisture in the sand also matters. Too much water can make steam, which causes bubbles or holes in the part. Too little water makes the sand weak, so the mold may fall apart.
Workers check the moisture level often. They use simple tools to test how much water is in the sand. They also watch how hard the sand packs. Keeping the right balance helps the mold stay strong and keeps the part close to the right size.
Tip: Regular checks on compaction and moisture help prevent many common casting problems.
Mold Stability
Mold stability means the mold keeps its shape from start to finish. Stable molds help parts come out with the right size and shape. If the mold moves or changes during pouring, the part may warp or shrink in the wrong way. Makers use strong sand casting materials and careful mold design to keep molds stable.
They also use lab tests to check for defects like porosity or inclusions. These problems can change the part’s size or make it weak. By checking molds and finished parts often, workers catch problems early and keep quality high.
Pattern Accuracy
Pattern accuracy is very important in sand casting. Each pattern makes a shape in the mold. This shape changes the size and look of the cast part. Engineers and workers watch pattern accuracy closely. Even small errors can make a part too big or too small.
Pattern Wear
Patterns get used many times in sand casting. Over time, the edges and surfaces wear down. This wear changes the mold’s shape. Parts may not fit the original size. Workers see that old patterns make rougher parts. Sometimes, there are bumps or uneven spots. These problems mean more work or even throwing parts away.
3D sand printing brings new problems. The sand layers do not always stick the same way. This can change how strong the mold is. It also changes the surface of the mold. When the mold’s surface changes, the part’s surface changes too. The size can also be off. Engineers use special tools to check these changes. They find that how sand prints and sticks can change the part’s size. Checking patterns often and fixing them helps keep parts the right size.
Shrinkage Allowances
Metals get smaller as they cool. Workers must plan for this by making patterns bigger. This extra size is called shrinkage allowance. If the allowance is too small, the part will be too small. If it is too big, the part needs more cutting.
The right allowance depends on the metal, mold, and process. For example, aluminum shrinks less than steel. Printed sand molds may need different allowances. This is because printing speed and resin can change the mold. Studies show that controlling mold strength and air flow helps shrinkage stay the same. This helps workers make parts the right size more often.
Note: Keeping patterns in good shape and using the right shrinkage allowance helps workers make parts that fit well. These steps also help stop waste and extra work.
Sand Casting Process Control
Pouring and Cooling
Sand casting needs careful steps during pouring and cooling. Workers check important things to keep parts the right size. The table below lists what workers watch and how it changes the part:
Process Control Benchmark | Description and Effect on Casting Dimensions and Properties |
---|---|
Pouring Temperature | Changes grain size and how the metal forms; lower temperatures make smaller grains and stronger parts. |
Mould Temperature | Controls how the metal freezes and cools, which changes the inside structure and keeps the size steady. |
Mould Material | Changes how heat moves and how the part cools, which affects the final size. |
Mould Cooling System | Controls how fast the part cools and how heat spreads, which helps keep the size right. |
Pouring Rate | Changes how heat moves and how the metal hardens, which affects the inside of the part and how strong it is. |
Rotational Speed of Mould | Helps spread metal evenly and makes the surface smooth; the best speed keeps the walls even, makes grains smaller, and stops mistakes. |
How fast the part cools and how long it takes to get hard are very important. These things change how the metal fills the mold. Factories use sensors to watch the temperature as the metal is poured and cools down. They also use computers to guess what the part will look like. Cooling curves show how fast the part cools and when it hits certain temperatures. These curves help workers see if the part will shrink or bend.
- Cooling curves tell how fast the part cools and when it gets to important temperatures.
- When the metal cools, steam can make some spots cool faster or slower, which can bend or crack the part.
- How heat moves depends on the mold, the cooling system, and the shape of the part.
- Computer programs use cooling data to guess if the part will be the right size and shape.
Handling and Vibration
How workers move and handle the mold can change the part’s size. Workers must be gentle before and after pouring. If the mold shakes or moves too much, the metal may not fill every space. This can make the part too big, too small, or bumpy. Shaking can also move the sand, which changes the mold’s shape. Factories teach workers to move molds carefully and use tools that stop shaking. Being careful helps keep the part close to the planned size.
Tip: Using steady hands and the right tools during sand casting helps stop mistakes and keeps parts the right size.
Mold and Core Placement
Alignment Issues
Mold alignment plays a key role in sand casting precision. When workers assemble the mold, they must line up the two halves exactly. Even a small shift can cause the part to have extra material, called a mismatch. This mismatch often leads to extra work during finishing. Industry standards set dimensional tolerances for sand casting at about ±0.020 inches per inch. This means that for every inch of the part, the size can change by this small amount and still meet quality rules.
Pattern makers use draft angles, usually between 1° and 3°, to help remove patterns from the sand without breaking the mold walls. These angles also help keep the mold shape true. Finer sand grains make smoother mold surfaces, which helps control the final size of the part. Workers check for flatness, roundness, and concentricity to make sure the part meets geometric tolerances.
Tip: Careful mold assembly and regular checks help prevent alignment problems and keep parts within the allowed size range.
Core Support
Cores create holes or special shapes inside cast parts. Workers place cores in the mold using core prints. These prints form small recesses that hold the core steady during pouring. If the core moves, the part may have the wrong shape or size inside. To stop this, workers use chaplets—small metal supports that keep the core in place when hot metal flows in.
Key points for core support in sand casting:
- Core prints must fit the core exactly to stop movement.
- Chaplets support heavy or long cores and prevent sagging.
- Machining allowances, usually 1.5 mm to 3 mm, are added to patterns. These extra amounts let workers finish the part to the right size after casting.
- Workers follow strict placement rules to keep the core in the right spot.
A well-supported core helps the part meet both shape and size requirements. Regular checks and good design keep the process reliable and the parts accurate.
Post-Casting Operations
Machining and Finishing
Machining and finishing steps help improve the final look and size of sand cast parts. Workers often remove extra material from casting surfaces to reach the right shape. They use tools like grinders, mills, and lathes to smooth rough edges. These steps also help fix small mistakes from the casting process. Sand casting surface treatments, such as shot blasting or sanding, make casting surfaces smoother and cleaner. These treatments remove sand, scale, and other marks left from the mold.
Some parts need extra sand casting surface treatments to meet special needs. For example, a part may need a coating to stop rust or wear. Machining and finishing also help reach tight size limits. Workers check the part after each step to make sure it matches the plan. Quality control teams watch these steps closely. They make sure every part meets the company’s standards for casting surfaces and size.
Inspection Methods
Inspection methods play a big role in quality control for sand casting. Workers use many tools to check if casting surfaces and sizes meet the plan. They use electronic devices like coordinate measuring machines (CMMs), dimensional scanners, and electronic hand tools. These tools measure the part’s size and shape. The Checkmaster CMM System checks dimensions with an accuracy of 0.0001 inches. It creates color-coded reports to show where the part is too big or too small. The Zeiss ATOS 5 Scanner captures millions of points on casting surfaces. It builds a 3D model to help with first article inspections.
Quality control teams follow control plans. These plans list what to check, how often to check, and what counts as a good part. Statistical Process Control (SPC) helps track changes in the process. It finds problems before they affect the final part. Workers must finish a final dimension report before they ship any order. This report proves that the part meets all size and casting surfaces rules. These steps help keep sand casting parts safe and reliable.
Common Defects
Sand casting can cause problems that change a part’s size and quality. The two main problems are warping, distortion, and mold shift. These problems make it hard for parts to fit the needed size.
Warping and Distortion
Warping and distortion change how a cast part looks. These problems happen when some areas cool faster than others. When cooling is not even, it causes stress in the metal. Hot tears are cracks that show up as the metal gets hard. Shrinkage cavities can form if the metal does not fill the mold before it gets solid. Both of these problems make the part weaker and harder to keep the right size.
Some things make warping and distortion more likely:
- Cooling rates that are not the same everywhere
- Bad mold design, like walls that are too thick or thin
- Gating and vents in the wrong places
- Changes in mold moisture or air in the area
- Vibrations from machines close by
Workers use 3D scanners and computer programs to find these problems early. Good control of the process and smart mold design help stop warping and keep parts the right size.
Mold Shift
Mold shift happens when the two mold halves do not match up. This makes a step or bump on the finished part. Mold shift often means the part is not the right size. The main reasons are loose clamps, worn pins, or rough handling.
To stop mold shift, workers check the mold before pouring metal. They use strong clamps and check tools often. Training helps workers see problems early. Keeping molds steady and lined up helps parts fit the size rules and need less fixing.
Tip: Paying close attention to mold design, putting molds together, and cooling helps stop common problems and makes it easier to meet tight size rules.
Improving Dimensional Accuracy
Best Practices
Custom sand casting can be more accurate by following good steps. In the past, many shops guessed how much to change pattern sizes. This guessing often meant more test runs and higher costs. Now, experts say to use computer models to see what the part will look like. These models help cut down on test castings and save resources.
Shops should pay attention to core materials and timing. The kind of core, how much resin is used, and how long the core stays in the mold all matter. Teams now study these things to make better shrinkage rules. Picking the right shrinkage number is important because it can change for each job. For example, permanent molds and sand cores need different shrinkage numbers.
Using standards like ISO, ASTM, or DIN helps keep results the same. Shops that watch their numbers and follow these rules make fewer mistakes in custom sand casting.
Using computer models, hands-on tests, and strict controls works best. Shops that do these things make parts that fit better and waste less.
Modern Tools
New technology has made custom sand casting better. Computer programs let engineers see how a part will shrink or change shape before making it. These tools use data about sand, resin, and heat to guess what will happen. Workers can change the process before pouring metal.
Shops also use sensors and scanners to check parts during and after casting. These tools measure the size and shape of each part. If something is wrong, workers can fix it fast. Training workers to use these tools is very important. Well-trained teams find problems early and keep custom sand casting working well.
Tip: Shops that buy new tools and train workers get better accuracy and save money over time.
Sand casting works best when workers watch each step closely. They need to use good materials and follow the right steps. Teams who want better parts should do these things:
- Pick strong sand and well-made patterns.
- Check how the mold is put together and lined up.
- Make sure the metal is poured at the right heat and cools slowly.
- Look over and finish each part carefully.
Teams get better by learning new skills and checking their work often. Even small changes in how they work can make parts better and help avoid errors.
FAQ
What is the main reason for size changes in sand cast parts?
Sand molds can shift or change shape when hot metal enters. This movement causes the final part to be bigger, smaller, or warped. Workers must control mold strength and pouring steps to reduce these changes.
How do workers check if a sand cast part meets size rules?
Workers use tools like calipers, micrometers, and 3D scanners. They measure key spots on each part. Quality teams compare these numbers to the plan. If a part does not match, they fix the process.
Can sand casting make very precise parts?
Sand casting usually cannot match the tight tolerances of die casting or investment casting. Most sand cast parts need extra machining to meet strict size rules. Shops use better sand and careful steps to improve accuracy.
What steps help prevent warping in sand casting?
Workers use even cooling, strong molds, and smart part design. They avoid thick and thin walls in the same part. Careful handling after casting also helps keep parts straight and true.