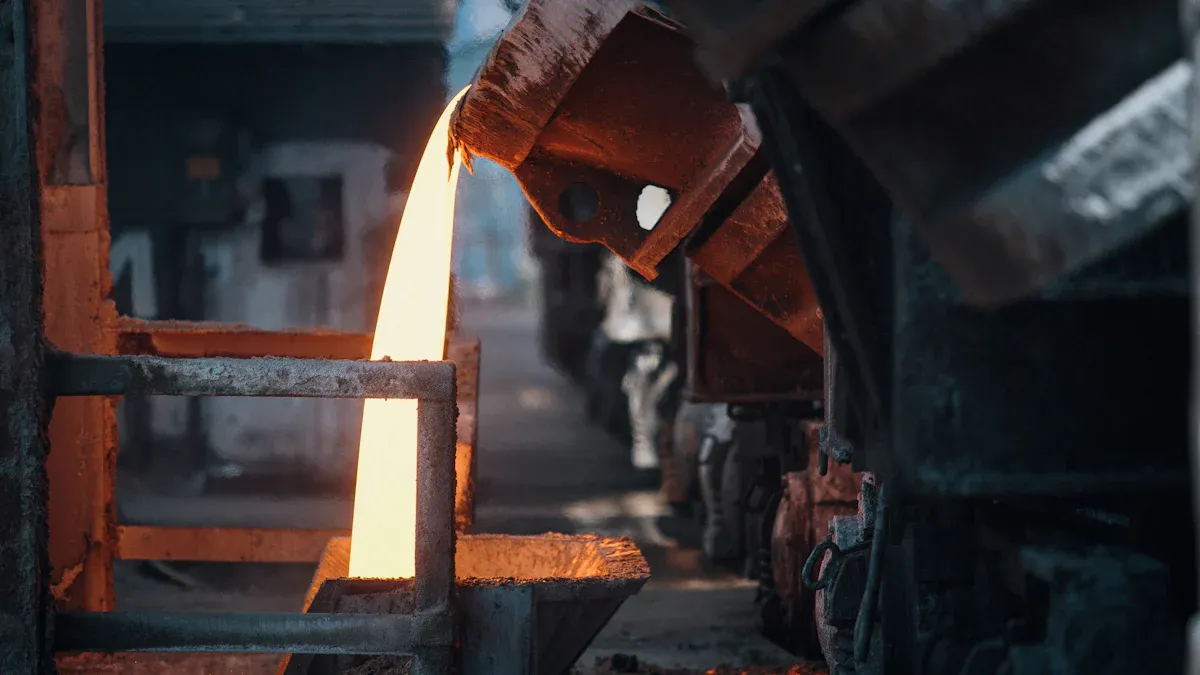
Sand casting does not use a mold that lasts forever. In sand casting, workers make a new sand mold for each part. Permanent mold casting uses a metal mold that can be used many times. The permanent mold method makes parts with a smooth surface and strong features. Each metal casting process has its own steps. Permanent molds last a long time, but sand molds are changed after each use.
Key Takeaways
- Sand casting uses a new sand mold for each part. This makes it flexible and cheap for small or custom jobs.
- Permanent mold casting uses a strong metal mold that can be used many times. It is good for making many parts with smooth surfaces and high strength.
- Sand casting is good for big or tricky shapes and many metals. But it gives rougher surfaces and needs more finishing work.
- Permanent mold casting makes parts faster with better accuracy and strength. But it costs more at first and is best for making many parts.
- Picking the right casting method depends on size, shape, how many you need, surface finish, and budget. This helps you get the best quality and value.
Sand Casting Overview
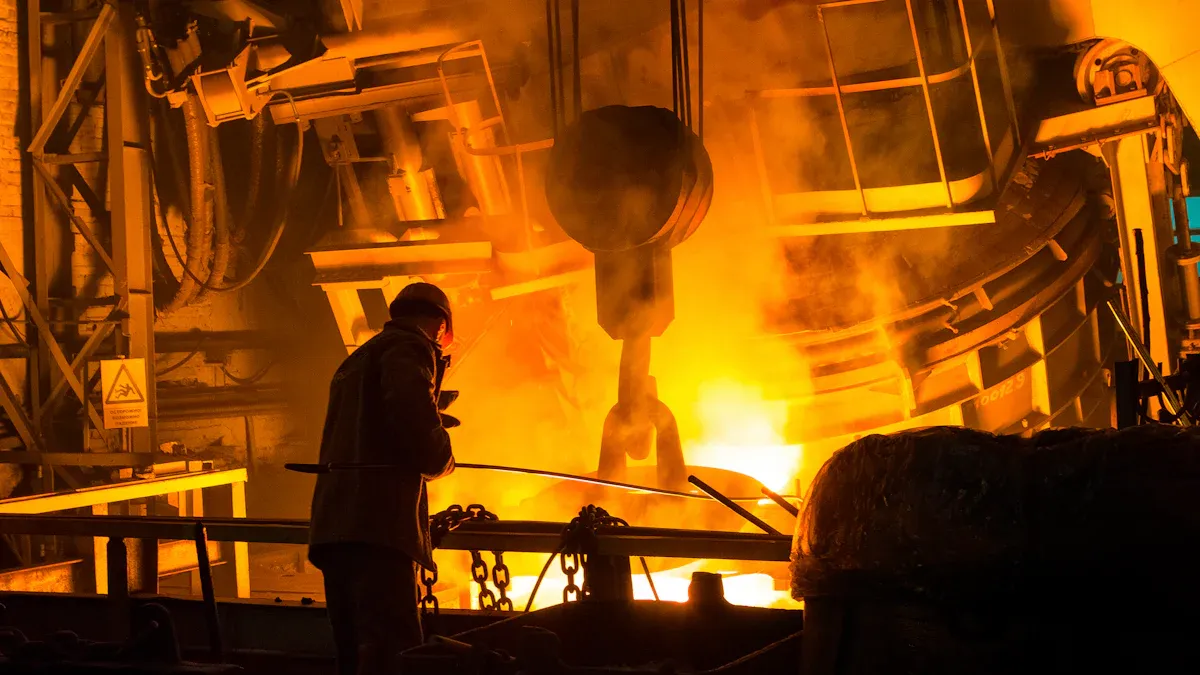
Process
Sand casting makes metal parts in several steps. First, workers make a pattern that looks like the part. The pattern is a little bigger because metal shrinks when it cools. Workers put sand around the pattern to make two mold halves. These halves are called the cope and drag. They take out the pattern and put the mold halves together. Hot metal is poured into the mold through special paths. The metal cools and gets hard inside the sand. When the metal is solid, workers break the mold to get the part out. They cut off extra metal pieces to finish the part.
A normal sand casting process has these steps:
- Pattern making
- Mold making
- Clamping
- Pouring molten metal
- Cooling and solidification
- Shakeout (breaking the mold)
- Trimming and finishing
Today, foundries use new tools like 3D printed sand cores. They also use computer programs to help make better parts. Sand casting is good for the environment because sand and metal can be used again.
Mold Characteristics
The mold in sand casting is made from sand shaped by a pattern. Sand molds do not cost much to make. It is easy to change the design if needed. Sand can make big or small shapes. Sand molds work with many metals like steel, aluminum, and titanium. Sometimes, clay or resin is mixed in to make the sand stronger. Mold features like green strength and flowability help keep the part the right size and shape. Each sand mold is used only once, so a new one is needed for every part.
Tip: Sand molds are great for making parts with thin walls or special holes.
Typical Applications
Sand casting is used in many jobs because it is flexible and not too expensive. Car companies use sand casting for engine blocks and other tricky parts. Airplane makers use it for small batches of magnesium and aluminum parts. Sand casting also helps make musical instruments, machines, furniture, and jewelry.
- Automotive: engine blocks, cylinder heads, transmission cases
- Aerospace: thin-walled housings, brackets, and cooling components
- Industrial: pumps, valves, and heavy machinery parts
- Other: sculptures, sporting goods, lighting fixtures, and toys
A new study found that 3D printed sand mold inserts can put codes on parts. These codes help companies track each part and check for problems. This makes it easier to follow parts through the supply chain and fix mistakes.
Sand casting is good for making tricky parts at a lower price. It works well for small or medium amounts of parts.
Permanent Mold Casting Overview
Process
Permanent mold casting uses a tough metal mold again and again. Workers pour hot metal, like aluminum, into the mold. The mold is made from strong metals like steel or cast iron. These metals do not crack from getting hot and cold many times. Gravity helps fill the mold, so it is called gravity die casting. The mold cools the metal fast and makes a smooth part. When the metal gets hard, workers open the mold and take out the part. The mold can be used again with little cleaning.
- Permanent mold casting uses molds that can be used many times.
- The molds are made from metals that melt at high temperatures.
- This process works best for metals like aluminum.
- Molds are made by CNC machines or other metal shaping tools.
- The process can use machines to help make many parts fast.
- Special molds or cores can be made with 3D printing for hard shapes.
Mold Characteristics
A permanent mold can last for hundreds or thousands of uses. Mold materials like steel or copper alloys can handle hot metal. The mold cools the metal fast and makes the part strong and smooth. The mold has special paths for metal and air to move. Clamps hold the mold tight when casting. Computer programs help design better molds. The mold cools the metal well, so the part is strong and has small grains.
Note: Permanent molds keep their shape well, so every part looks the same.
Typical Applications
Permanent mold casting is used when many parts must look the same. Car makers use it for wheels, pistons, and gears. Airplane makers use it for light parts like brackets. It also makes parts for pumps, lights, and sports gear. Permanent mold casting is best for making many good parts at once.
Key Differences: Sand Casting vs Permanent Mold
Mold Type
Sand casting uses a mold made from sand. Workers make a new sand mold for each part. This makes it easy to change the design. Sand molds work for big or small parts. The sand mold is thrown away after one use. Permanent mold casting uses a metal mold. The metal mold can be used many times. It is made from steel or other strong metals. The metal mold keeps its shape for a long time. The table below shows how casting methods are different in mold type, tolerance, and cost:
Casting Process | Mold Type | ISO 8062 CT Grade | Linear Tolerance (% of dimension) | Tolerance on 100 mm (mm) | Surface Finish (Ra, µm) | Tooling Cost Range (USD) |
---|---|---|---|---|---|---|
Green-Sand Casting | Expendable Mold | CT11–CT14 | ±0.5–2.0% | ±0.5–2.0 | 6–12 | Low (< $500 per pattern) |
Chemically-Bonded Sand | Expendable Mold | CT9–CT12 | ±0.3–1.2% | ±0.3–1.2 | 3–6 | Moderate |
Die Casting (Hot & Cold Chamber) | Reusable Mold | CT1–CT4 | ±0.05–0.3% | ±0.05–0.3 | 0.5–1.5 | Very High ($10,000–$200,000) |
Gravity & Low-Pressure Die Casting | Reusable Mold | CT2–CT6 | ±0.1–0.5% | ±0.1–0.5 | 1–4 | High |
Note: Sand casting uses molds that are used once. Permanent mold casting uses metal molds that last a long time. Metal molds cost more but can be used again and again.
Surface Finish
Surface finish means how smooth the outside of a part is. Sand casting usually makes a rougher surface. This is because the sand leaves marks on the part. Permanent mold casting makes a smoother surface. The metal mold is hard and smooth. This helps the part look better and need less polishing.
- Sand casting surface roughness changes with sand, water, and pouring speed.
- The best sand casting uses less water, slow pouring, and high heat.
- This can make the surface as smooth as 5.8 µm.
- Permanent mold casting usually makes a smoother surface, between 0.5 and 4 µm Ra.
- The mold, sand, and pouring all change the final surface.
- Permanent molds help stop problems like holes and sand spots.
Tip: Permanent mold casting is best for parts that need a smooth surface.
Mechanical Properties
Mechanical properties tell us how strong and hard a part is. Sand casting can make strong parts. But the metal cools slower in sand casting. This makes bigger grains inside the metal. Bigger grains can make the part weaker. Permanent mold casting cools metal faster. This makes smaller grains and a stronger part.
Test Type | Description | Key Findings (Sand Casting) | Key Findings (Permanent Mold) |
---|---|---|---|
Dimensional Deviation | Accuracy of part size | 0.08–0.10 mm deviation | Tighter control, less deviation |
Ultimate Tensile Strength | How much force before breaking | 31%–42% lower than permanent mold | Higher strength, less porosity |
Hardness | Resistance to scratching/denting | 17–56 HRB (depends on sand type) | Higher, more consistent hardness |
Permanent mold casting often makes parts that are stronger and harder. The fast cooling helps stop problems and makes the part last longer.
Cost and Volume
Cost and how many parts you need are important. Sand casting costs less to start. It is good for small batches or testing new ideas. Permanent mold casting costs more at first. The metal mold is expensive to make. But if you make many parts, the cost per part goes down.
- Sand casting: Cheap molds, good for small or medium jobs, easy to change designs.
- Permanent mold casting: Expensive molds, best for making lots of parts, cheaper per part if you make many.
- Permanent molds save money if you need thousands of parts.
Note: Companies pick sand casting for custom or small jobs. They use permanent mold casting for big jobs and when they want better parts.
Pros and Cons
Sand Casting
Sand casting has many good points for companies. It can make big and tricky shapes easily. Changing the design is simple and fast. This method is great for making a few parts at a time. The tools do not cost much, so it saves money on new ideas or special orders. Sand molds can be used again, which is better for the planet.
But sand casting also has some problems. Each mold is used only once, so workers must make a new one every time. The outside of the part is rougher than with other ways. Parts often need more work to get the right size and shape. It is not as exact, with about 0.030 inches difference for the first inch. Problems like holes or shrinking can happen if the sand is not packed well or the metal is too hot. Making tricky parts takes more time, so workers may cost more.
Tip: Sand casting is a good pick if you want to save money, need parts fast, or want to change designs. But it is not the best for parts that must be very smooth or exact.
Benefit / Drawback | Description |
---|---|
Cost-effective | Cheap tools and materials for small or medium jobs |
Design flexibility | Can make big, tricky shapes with many metals |
Short lead times | Quick to set up and start making parts |
Lower accuracy | Rougher outside, needs more work to finish |
Defect risk | Can get holes, cracks, or other problems |
High labor for complexity | More worker time needed for hard shapes |
Permanent Mold Casting
Permanent mold casting uses tough metal molds that last a long time. This way makes parts that are very close in size, about 0.015 inches off for the first inch. The outside is smooth, and the parts are strong with fewer problems. It is fast, so it works well for making lots of parts. This method is best for metals like aluminum.
There are some downsides too. The mold and machines cost a lot at the start. It is not a good choice for making just a few parts. The mold cannot make very big parts. Some shapes may need extra work where the mold comes apart. Not all metals can be used with this way.
Factor | Permanent Mold Casting |
---|---|
Mold durability | Can use the mold thousands of times |
Surface finish | Smooth, needs little extra work |
Dimensional accuracy | Very close in size, not much difference |
Production speed | Fast, good for making many parts |
Initial cost | High cost for tools and machines |
Size and material limits | Cannot make very big parts or use all metals |
Note: Permanent mold casting is best for companies that need many parts that look the same and can pay more for strong molds.
Choosing a Process
Application Needs
Picking the right casting process starts with knowing what the part must do. Some parts need to be very strong. Others need to look smooth or have special shapes. Medical parts often need to be exact and smooth. Car parts must be strong and made in big amounts. The table below shows which casting method is good for each job:
Casting Process | Main Benefits | Typical Applications |
---|---|---|
Vacuum Casting | High detail, smooth finish, fewer defects | Medical parts, precise auto parts, fine art pieces |
Squeeze Casting | Strong, dense, good heat flow | Electronics, strong auto parts, aerospace components |
Slush Casting | Low cost, fast, flexible designs | Decorative items, lamp bases, toys |
Rotational Casting | Even thickness, low cost, many shapes | Tanks, dolls, car air ducts |
Hot Isostatic Pressing | Better material, less porosity, works for metals/ceramics | Aerospace, medical implants, turbine blades |
Investment Casting | Very precise, many materials, smooth finish | Turbine blades, medical, special auto parts |
Shell Molding | Accurate, stable, smooth surface, good for many parts | Auto parts, aerospace, gear housings |
Electroslag Casting | High quality, good for big, thick parts | Turbine shafts, power rotors |
Die Casting | Fast, precise, strong | Gearbox cases, electronics, appliance parts |
Pressure Die Casting | Very fast, accurate, smooth | Wheels, engine blocks, electronics |
Centrifugal Casting | Strong, many shapes, cost-effective | Pipes, rings, special casings |
Permanent Mold Casting | Accurate, smooth, repeatable | Pistons, gears, machinery parts |
Gravity Die Casting | Smooth, efficient, cost-effective | Wheels, hardware, large art |
Low-Pressure Casting | Good material, high yield, less porosity | Aerospace, complex auto parts, machinery |
Continuous Casting | Efficient, smooth, cost-effective | Steel slabs, tubes, pipes |
Note: What the part needs helps pick the process. For example, sand casting is good for big, tricky shapes that do not need to be very smooth.
Some jobs, like in power plants, have strict rules for parts. Foundries must check quality and use the right process. This makes sure parts work well under heat and stress. Technical checks help match the process to the job.
Production Volume
How many parts are needed also changes the choice. Some casting ways are best for small batches. Others are better for making thousands of parts. Sand casting is good for small or medium amounts. It is easy to change the design and costs less to start. When companies need lots of the same part, they pick die casting or permanent mold casting.
Modern factories use smart tools to watch and improve casting. They collect data from machines to check quality and fix problems fast. Studies show using real-time data helps companies pick the best casting method. This makes more parts and less waste, especially for big jobs.
Tip: If you need just a few custom parts, pick a flexible process. For lots of parts, choose a process that is fast and makes less waste.
Cost Considerations
Cost is a big part of picking a casting process. Companies look at money needed at the start and the cost for each part over time. A process like sand casting is cheap to start but may cost more per part if making thousands. Permanent mold casting costs more at first but saves money if making many parts.
To decide, companies use ROI (Return on Investment) to compare costs and benefits. They look at:
- All costs and savings now and later.
- How long it takes to get the money back.
- Risks, like mistakes or delays.
- How many people want the part and what it sells for.
- The cost of borrowing money.
- The total cost for the part’s whole life, not just the first price.
Companies often see that a process with a higher starting cost is better if it makes good parts faster and with fewer problems.
A real example shows sand casting may be cheaper at first. But if there are more mistakes or extra work, it can cost more later. Companies must balance setup costs, part quality, and how many parts they need.
Sand casting and permanent mold casting are different in important ways.
- Sand casting needs a new sand mold for every part. Permanent mold casting uses the same metal mold again and again.
- Sand casting is good for special shapes and small numbers of parts. Permanent mold casting is better for making lots of parts with smooth surfaces.
If you need a few special parts, sand casting is flexible. If you want many parts that look nice, permanent mold casting works best.
FAQ
What metals work best with sand casting?
Sand casting works well with many metals. Foundries often use aluminum, iron, steel, bronze, and brass. This process handles both ferrous and non-ferrous metals. Workers choose the metal based on the part’s strength, weight, and cost needs.
Can permanent mold casting make large parts?
Permanent mold casting usually makes small to medium parts. The metal molds are heavy and expensive to build for large items. For very big parts, sand casting is a better choice.
How does surface finish compare between the two methods?
Permanent mold casting gives a smoother surface than sand casting. The metal mold creates fewer marks and defects. Sand casting leaves a rougher finish because of the sand texture.
Is sand casting more environmentally friendly?
Sand casting can be more eco-friendly. Workers often reuse sand and recycle leftover metal. This process uses less energy for small batches. Permanent mold casting also recycles metal, but the molds need more resources to make.
Which process is faster for high-volume production?
Permanent mold casting works faster for high-volume jobs. The reusable metal mold speeds up the process. Sand casting takes longer because workers must make a new mold for each part.