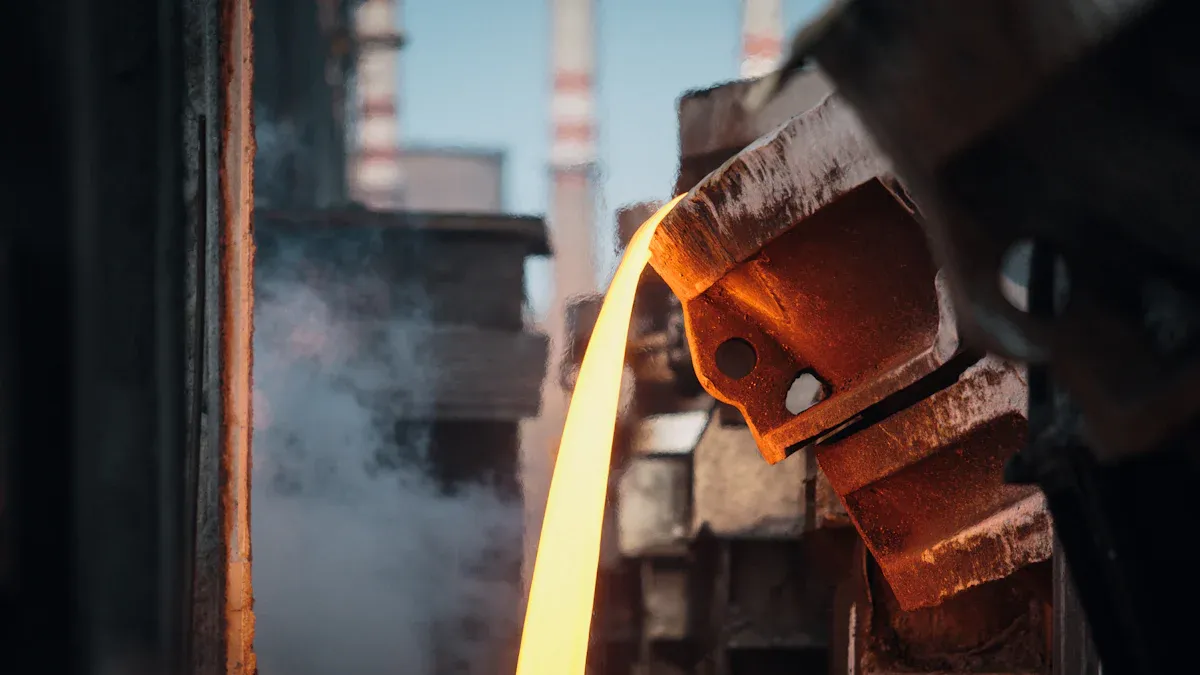
You can get better results in investment casting by using some easy rules. Pick smooth changes and make your designs simple. Do not add extra things that make the process harder. Every good choice helps you get parts that are better and cost less.
Remember: Simple designs cause fewer problems and make manufacturing easier.
Key Takeaways
- Make sure the wall thickness is the same everywhere on your part. This helps stop cracks and other problems.
- Pick rounded edges, not sharp corners. This spreads out stress and stops breaks.
- Choose tolerances and surface finishes that fit what your part needs. This can help you save time and money.
- Use simple and smooth shapes. Do not add hard or tricky features. This makes casting easier and better.
- Talk with foundry experts early. This helps you fix your design and avoid problems.
Wall Thickness
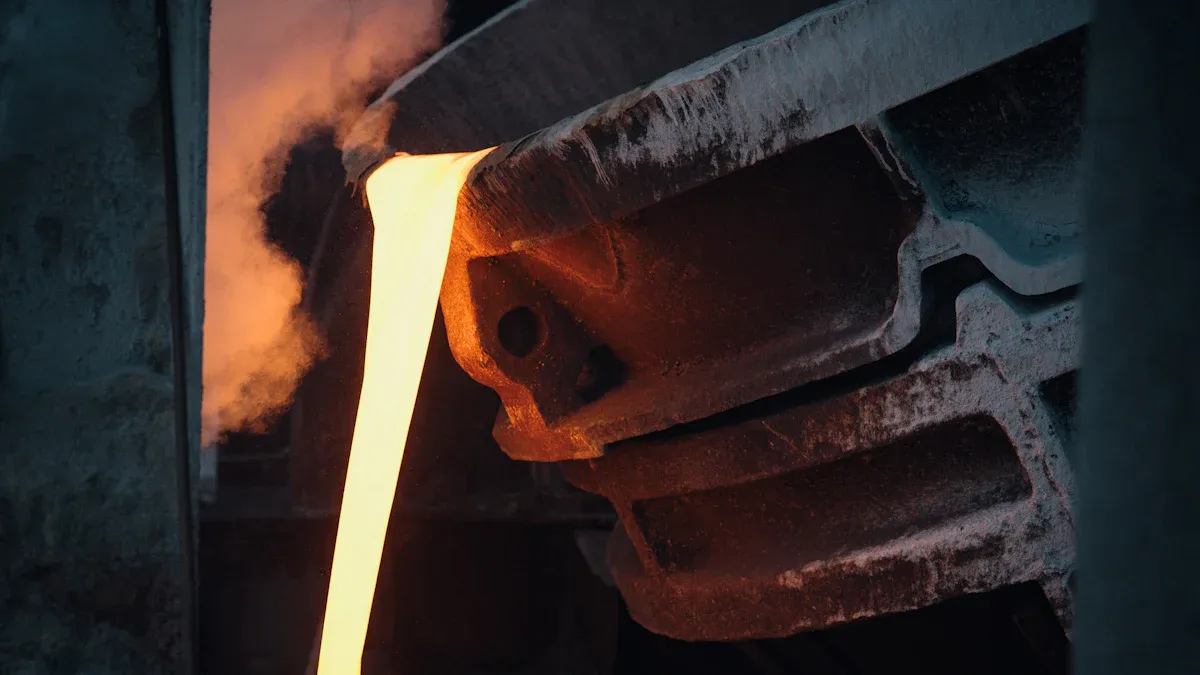
Uniformity
You should always keep wall thickness as uniform as possible in investment casting. When you use even wall thickness, you help prevent many common problems. Uneven walls can cause stress and cracks during cooling. If one part of your casting is thicker than another, it cools at a different rate. This can lead to warping or even breaking.
- Studies show that non-uniform shell thickness creates stress and thermal problems. These issues can cause cracks and deformation.
- CT scans of cast parts reveal that changes in wall thickness make it hard to control the final shape.
- Thicker or uneven areas slow down cooling. This can cause the shell to break or the part to lose its shape.
- Thin areas, especially at corners, often have more stress and are more likely to have defects.
- Adjusting the angles and sizes of your wax patterns can help you keep wall thickness even. This leads to better quality and fewer defects.
Tip: Uniform wall thickness improves the strength and accuracy of your investment casting parts.
Minimums and Maximums
You need to follow some basic rules for wall thickness in investment casting. The American Casting Company says that the minimum wall thickness depends on the metal you use and how well the molten metal flows. You should keep the walls uniform or slightly tapered. This helps the metal fill the mold and solidify from thick to thin sections. Feeding from thick to thin areas helps avoid problems like porosity.
Here is a table with common guidelines:
Parameter | Minimum Value | Optimal Range |
---|---|---|
Minimum Wall Thickness | 1.0 mm | 5 to 15 mm |
If you make walls too thin, the metal may not fill the mold. This can cause holes or weak spots. If you make walls too thick, the part may cool unevenly. This can cause cracks or other defects. Try to avoid heavy, isolated thick sections and do not let many thick sections meet at one point. This helps keep your investment casting strong and reliable.
Investment Casting Tolerances
Standard Ranges
You should know what tolerances are normal in investment casting. Tolerances show how much a part’s size can change from the plan. Most investment casting can keep linear tolerances from ±0.005 inch (0.13 mm) to ±0.015 inch (0.38 mm) for each inch of length. These numbers change based on your part’s size and shape. Smaller parts often have tighter tolerances. Bigger or more complex parts may need looser tolerances.
Tip: Asking for very tight tolerances can make your part cost more and take longer to make.
Industry studies say you can get tolerance grades (DCTG) from 4 to 8 with investment casting. This is close to what some advanced 3D printed core methods can do. Most changes in size come from how people handle the parts after casting, not from the casting itself. You can get better results by controlling what happens after casting and using machines to help.
Material Considerations
The metal you pick changes what tolerances you can get. Some alloys, like 17-4 and 15-5 PH steels, have been tested by the American Foundry Society. Their tests give you good data about how these metals act. This helps you set tolerances you can trust and not add extra safety margins.
Wax patterns are also important for investment casting tolerances. Wax can shrink and change shape as it cools, which changes your part’s final size. Scientists have measured how wax acts and use this to guess how much a part will shrink. This helps you set better tooling allowances and get more exact castings.
When you pick tolerances, try to balance quality and cost. If you want the tightest tolerances, you might pay more and wait longer. Pick tolerances that work for you but do not make the process too hard.
Radii and Corners
Rounded Edges
You should always use rounded edges when you design parts for investment casting. Rounded edges, also called fillets, help your parts last longer and stay strong. When you add a small radius, like 0.5 mm, you spread out the stress over a bigger area. This makes your part less likely to crack or break.
- Rounded edges distribute stress more evenly. This helps prevent cracks, deformation, and even fatigue failure.
- Fillets stop sharp changes in the shape of your part. These sharp changes often cause weak spots.
- You see fillets in gears, shafts, and pressure vessels because they need to be strong and last a long time.
- Fillets also help stop defects like porosity. They make it harder for voids or small holes to cause problems.
- Compared to chamfers, fillets give better stress distribution and make your part safer by removing sharp edges.
- Smooth, curved transitions help coatings stick better and reduce edge wear.
Tip: Adding fillets may make the mold a bit more complex, but the benefits for strength and quality are worth it.
Avoid Sharp Corners
You should avoid sharp corners in your investment casting designs. Sharp corners create stress risers. These are places where stress builds up and can cause cracks or breaks. When molten metal fills the mold, sharp corners cool faster than the rest of the part. This can lead to defects like cracks, warping, or even incomplete filling.
Sharp corners also make it harder to remove the part from the mold. They can damage the mold or the part itself. If you use rounded corners instead, you help the metal flow better and reduce the risk of defects.
Note: Always check your design for sharp corners and replace them with small radii. This simple step improves the quality and life of your investment casting parts.
Surface Finish
Typical Results
Investment casting gives parts a smooth surface. Most parts come out with a fine texture. They often do not need extra work. The process makes surfaces with roughness between 63 and 125 microinches (1.6 to 3.2 micrometers). This finish is good for many products.
- Near-net-shape parts mean less machining is needed.
- Wax patterns help make detailed and clean surfaces.
- Most foundries can make many parts with the same finish.
Tip: If you want a smoother finish, ask for polishing or machining. This will take more time and cost more.
Over-Specification
Do not ask for a finer surface finish than you need. If you want a very fine finish, your part will cost more. The process may need extra tools or more hand work. It may also need more steps after casting. These things slow down production and make it more expensive.
Studies show that every extra finishing step adds to the cost. You pay more for materials, machine time, and labor. If you only ask for the finish you need, you save money. Investment casting already gives a good surface, so you do not need more most of the time.
Note: Asking for a finer finish can make your part cost more. It may not make your part better. Always match your needs to how the part will be used.
Surface Finish (Ra) | Typical Use Case | Extra Processing Needed? |
---|---|---|
125 µin (3.2 µm) | Most industrial parts | No |
63 µin (1.6 µm) | Decorative, visible | Sometimes |
< 32 µin (0.8 µm) | High-precision surfaces | Yes |
You get the best results when you balance your needs with what investment casting can do. This saves money and helps your project run well.
Part Size and Weight
Size Limits
You need to know the practical size limits for investment casting. Most foundries can make parts that fit in your hand or on a small table. The typical maximum size for a single investment casting part is about 24 inches (600 mm) in length. Some foundries can go a bit larger, but you get the best results with smaller parts.
- Small parts: Investment casting works very well for small, detailed parts. You can make parts as small as a few grams.
- Medium parts: Most foundries can cast parts up to 50 pounds (about 23 kg).
- Large parts: Some foundries can make parts up to 200 pounds (about 90 kg), but you may see more defects and higher costs.
Tip: Always check with your foundry about their size limits before you start your design.
Part Size | Typical Range | Best Quality |
---|---|---|
Small | < 1 lb (0.5 kg) | Excellent |
Medium | 1–50 lbs (0.5–23 kg) | Very Good |
Large | 50–200 lbs (23–90 kg) | Good |
Weight Considerations
You should also think about the weight of your investment casting parts. Heavy parts can cause problems during casting and cooling. If you design a part that is too heavy, you may see more shrinkage, cracks, or warping. Lighter parts cool faster and have fewer defects.
- Avoid oversized features that add extra weight.
- Try to keep your part’s weight as low as possible for its function.
- If you need a heavy part, ask your foundry for advice. They may suggest changes to your design.
Note: Lighter parts are easier to handle, ship, and install. You save money and get better quality.
You get the best results when you design parts that fit within the common size and weight limits for investment casting. This helps you avoid defects and keeps your costs down.
Gating and Risers
Gate Placement
You need to think carefully about where you place gates in your investment casting design. Gates are the channels that let molten metal flow into the mold. The best place for a gate is on the thickest section of your part. When you do this, you help the metal flow smoothly and fill the mold without problems.
Research shows that placing gates at or near the thickest sections improves metal flow and feeding during solidification. If the gate is as thick as the casting section, the molten metal moves in a calm, steady way. This helps you avoid turbulence, which can cause defects. A thick gate also stays liquid longer than the rest of the part. This means it can keep feeding metal into the casting as it cools and shrinks. You get fewer holes and less porosity.
Engineering guidelines also say that gates on thick sections reduce sink marks and make finishing easier. You avoid putting gates in high-stress areas, which helps your part stay strong. Always try to taper the gate from thick to thin. This lets the metal flow from the thickest part to the thinner areas, filling every space.
Tip: Place gates on the thickest sections and taper them toward thinner areas for the best results.
Riser Use
Risers play a key role in investment casting. A riser is a reservoir that holds extra molten metal. As your casting cools, it shrinks. The riser feeds more metal into the part so you do not get empty spaces or shrinkage defects.
Numerical simulations show that a well-designed riser, like a conical shape, makes sure the riser solidifies last. This is what you want. If the riser stays liquid longer, it keeps feeding the casting until it is solid. You avoid shrinkage flaws and get a defect-free part. If you change the pouring temperature or speed, you might get defects, so always follow best practices for riser design.
You should place risers close to the thickest sections. This helps the metal flow where it is needed most. The right riser placement depends on the metal you use and the shape of your part. Ask your foundry for advice if you are not sure.
Note: Proper riser placement and design help you get strong, high-quality investment castings every time.
Simplicity in Investment Casting Design
Avoid Complexity
Simple designs work best in investment casting. When you keep your part easy to make, you lower costs and get better results. Complex shapes need special tools and more labor. This makes your project more expensive and can slow down production. If you add too many small details or tricky features, you may face problems during casting. For example, undercuts are not possible with this process. You should avoid them in your design.
- Parts with simple, round shapes are easier to cast.
- Rotational symmetry helps the metal flow and fill the mold.
- Sharp corners and deep grooves can cause defects or cracks.
- Complex shapes often need extra machining, which adds time and cost.
Tip: Always ask yourself if each feature is needed. If not, leave it out to make your part easier to cast.
Streamlined Shapes
You should use smooth, flowing shapes in your investment casting designs. Streamlined parts help the metal move through the mold without getting stuck. Large corner radii spread out stress and make your part stronger. Draft angles of at least 1° help you remove the part from the mold without damage. Keeping section thickness within the recommended range also helps you avoid defects.
- Use large, rounded corners instead of sharp edges.
- Place parting lines away from critical areas to improve quality.
- Make sure your design fits within the size limits for investment casting.
- Add machining allowances to keep your part accurate after casting.
Note: Streamlined shapes not only look better, but they also make your part stronger and easier to produce.
When you keep your design simple and smooth, you get better quality and save money. Investment casting works best when you avoid unnecessary complexity and focus on what matters most.
Castability
Geometry
When you design for investment casting, think about the shape. The way your part looks changes how metal fills the mold. Simple shapes with smooth curves help metal flow better. If your part has a lot of details or is very complex, it needs extra care. Things like the size of struts, how many joints there are, and the angle of struts can change how metal moves. Sharp angles or thin spots can cause more problems.
- Lattice designs with tiny struts or lots of joints make casting harder.
- The gating system, like sprues and runners, controls how metal gets into the mold.
- If the gating is not balanced, metal may flow unevenly and cause defects like porosity.
- Mold flow simulations let you see where problems might happen before making the part.
The shape of your pattern also affects how close your final part is to your design. If you use a detailed wax pattern, you can get a very exact casting. Always check your design for places that might trap air or make the metal cool too fast.
Tip: Use smooth changes and avoid sudden thickness changes to help castability.
Collaboration
You get the best results when you work with foundry experts. These people know how to find problems in your design before casting starts. They can suggest changes to make your part easier to cast and less likely to have problems.
- Foundry experts help you pick the right gating and riser setup.
- They use simulations to test your design and find weak spots.
- Working together helps you balance printability, castability, and strength.
Share your design early in the process. Ask questions and listen to advice. This teamwork helps you avoid mistakes and get high-quality investment casting parts.
Note: Working with your foundry early saves time, lowers costs, and makes your product better.
You can get better results in investment casting by using these easy tips:
- Make sure the wall thickness stays the same everywhere.
- Add rounded edges and do not use sharp corners.
- Pick tolerances and surface finishes that make sense for your part.
- Keep your shapes simple and do not add tricky features.
- Talk and work with foundry experts to help your project.
Remember: Simple designs and good teamwork make castings stronger and more dependable. Try these tips in your next project to get the best results.
FAQ
What is investment casting best used for?
You should use investment casting for parts with complex shapes, fine details, or smooth surfaces. This process works well for small to medium-sized metal parts that need high accuracy.
How do you choose the right metal for investment casting?
You need to think about strength, corrosion resistance, and cost. Ask your foundry for advice. They can help you pick the best metal for your part’s needs.
Can you make large parts with investment casting?
You can make parts up to about 200 pounds (90 kg), but smaller parts give better results. Large parts may have more defects and cost more to produce.
How do you reduce defects in investment casting?
Tip: Keep wall thickness uniform, use rounded edges, and avoid sharp corners. Work with your foundry to review your design. Good planning helps you get strong, defect-free parts.