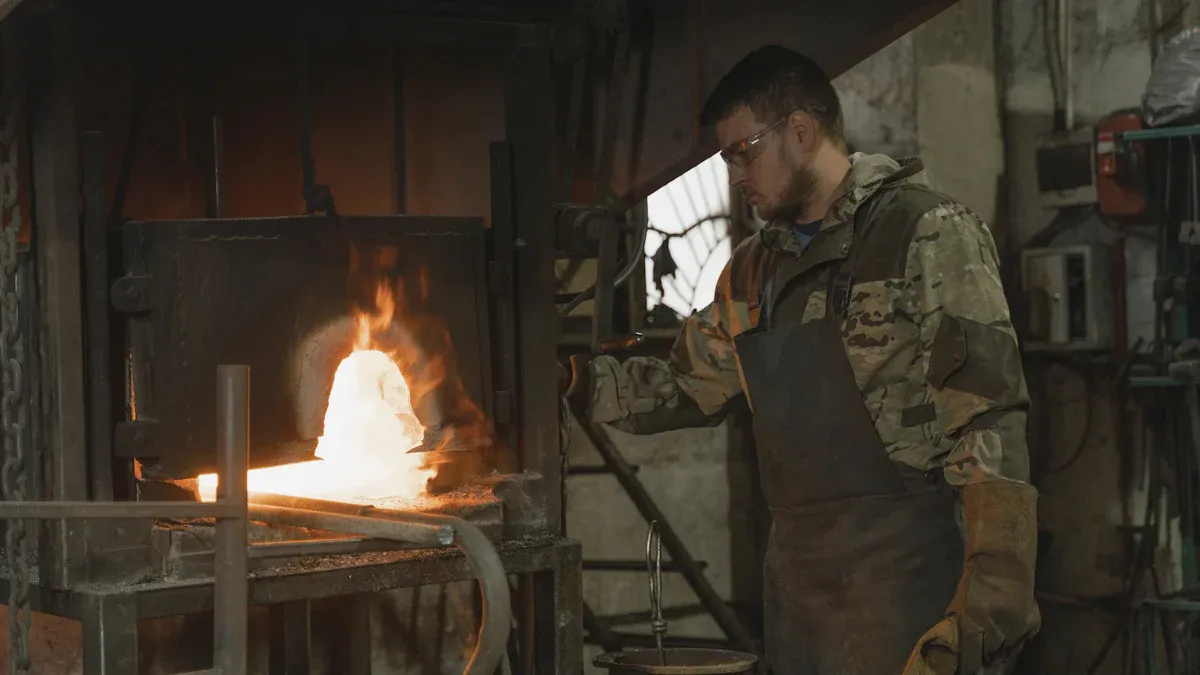
Investment casting utilizes a variety of materials to create precise and durable parts. Common materials include aluminum alloys, stainless steel, carbon steel, alloy steel, copper alloys, nickel-based and cobalt-based superalloys, as well as ceramics for molds. Each material group offers unique properties; for instance, aluminum is lightweight and strong, while stainless steel resists rust effectively. Selecting the right metals or alloys in investment casting significantly impacts both the performance of the parts and their overall cost. The melting phase alone can account for up to 39% of the total cost due to the material’s weight and price.
Cost Phase | Percentage of Total Cost (%) |
---|---|
Melting | 32 – 39 |
Among these, stainless steel is the most commonly used material in investment casting, especially for parts requiring high precision. Aluminum and copper alloys are also frequently chosen for applications needing lightweight components or electrical conductivity. Each material is best suited for specific uses, such as aerospace components or medical instruments, highlighting the versatility of investment casting.
Key Takeaways
- Picking the best metal or alloy in investment casting makes parts stronger. It also helps them fit better and cost less to make.
- Stainless steel is used a lot because it does not rust. Aluminum alloys are good for making light parts. Superalloys work well when things get very hot.
- Ceramic molds and wax patterns help make shapes with lots of detail. They also help parts have smooth surfaces and exact sizes.
- Testing materials helps use less and keeps quality high. This saves both money and resources.
- Different industries choose metals for what they need. Some need strength, some need heat resistance, and some need protection from rust.
Investment Casting Process
The investment casting process is also called lost-wax casting. It makes metal parts with exact shapes. First, a wax pattern is made. This pattern is covered with a ceramic shell. Then, hot metal is poured into the mold. Many materials can be used, like metals and ceramics. This helps make parts with tricky shapes and close measurements. The process starts with a wax model. The ceramic shell is built around the wax. The wax melts away, leaving a space for the metal.
Material Selection
Picking the right material is very important. It affects how good, strong, and costly the part is. Each job needs a material that fits its use. Stainless steel does not rust easily. It is good for medical and food parts. Aluminum alloys are light and strong. They work well in cars and planes. Nickel and cobalt superalloys can handle high heat. They are used in turbine blades.
Some things to think about when picking materials are:
- The part must be strong and tough enough.
- It should not rust in tough places.
- The size must be right, and it should not shrink too much.
- It should be easy to shape and finish.
- The cost and how well it works must be balanced.
Tools like spectrometers and tensile testers check the materials. They make sure each batch is good enough. Good material choices can cut waste by 15-20%. They can help use 85-90% of the material. Scrap can go down to 5% or less. This means better quality and less waste.
Mold Materials
The mold material changes how smooth and exact the part is. A wax pattern is used to make a ceramic shell. This shell is the mold for the metal. Polyurethane and silicone are used to make the first wax model. Polyurethane molds make wax patterns that shrink about 1.0%. This gives better size accuracy. Silicone molds can make more detailed shapes and smoother parts. But they shrink more, about 2.2%.
Mold Material | Average Shrinkage (%) | Performance Notes |
---|---|---|
Polyurethane | 1.0 | Accurate, less distortion, better for tight tolerances |
Silicone | 2.2 | Better surface finish, supports complex shapes, higher shrinkage |
Mistakes during dipping can make the part smaller by 0.2–0.4%. Special machines check the size at each step. The process uses equipment very well, up to 95% of the time. Recycling is important. The industry tries to reuse 80% of materials. This saves money and helps the planet.
Note: The lost wax casting method lets people use special alloys and ceramics. This makes it possible to create parts for tough jobs like planes, cars, and medical tools.
Investment Casting Materials
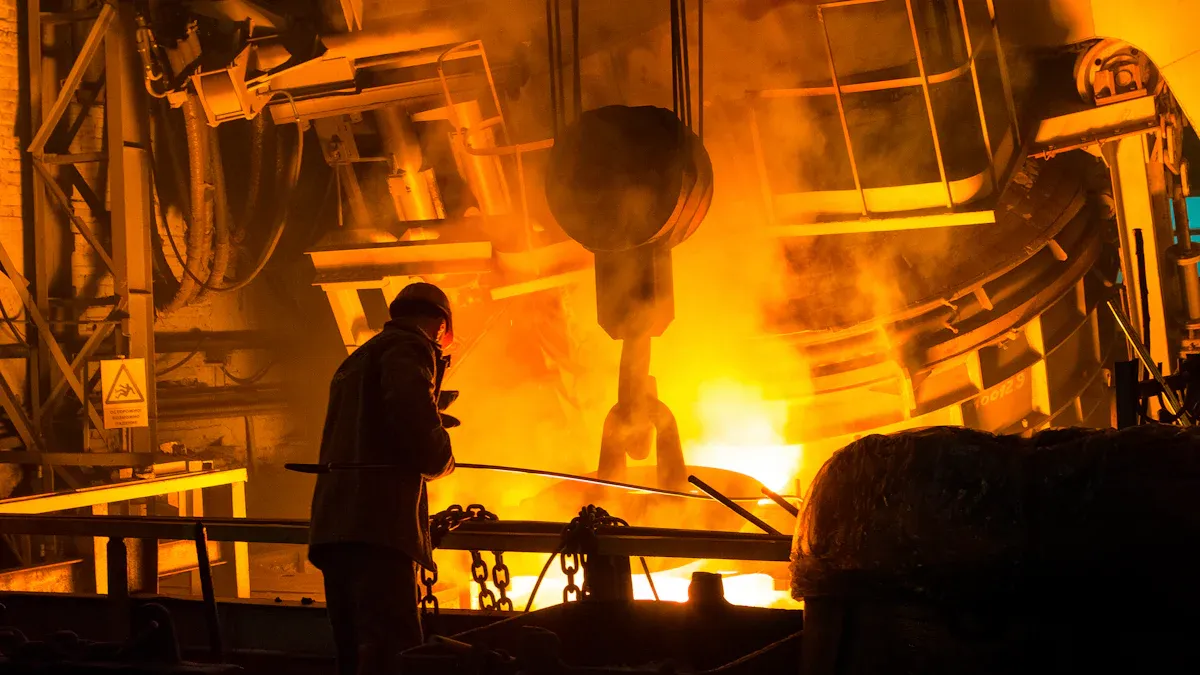
Investment casting uses many metals and alloys. Each group has special features for different jobs. The material you pick changes how strong, heavy, or costly the part is. The table below shows how common metals and alloys compare:
Property | Carbon Steel | Stainless Steel | Aluminum | Nickel-Based Alloys | Copper-Based Alloys |
---|---|---|---|---|---|
Corrosion Resistance | Low | High | Medium | High | High |
Wear Resistance | Medium | Low | Low | Low | High |
Tensile Strength | Medium | Low | Low | Medium | Low |
Hardness | Medium | Low | Low | Medium | Low |
Machinability | Medium | Low | High | Low | High |
Price | Low | High | Medium | High | Medium |
Aluminum Alloys
Aluminum is a top choice for investment casting. It is light and easy to shape. It also moves heat well. Pure aluminum moves heat at 235 W/m·K. This helps cool things down. Aluminum alloys are good for strong, light parts. High-grade aluminum is used in planes, cars, and electronics. It makes things lighter but still strong. Companies like Nu-Cast use aluminum casting for defense parts. These include electronic chassis and camera bodies. Aluminum can make thin walls and tricky shapes. This is great for making exact parts.
Stainless Steel
Stainless steel is popular because it does not rust. It is used for medical tools, food machines, and boat parts. Stainless steel is about 2.5 times heavier than aluminum. This makes it heavier but also stronger. It gives a smooth finish and works in tough places. People pick stainless steel when parts must last and stay clean.
Carbon and Alloy Steel
Carbon steel and alloy steel are both used a lot. Carbon steel is strong and costs less than stainless steel. It is used for gears, valves, and machines. Alloy steel has extra elements added. This makes it stronger and tougher. Alloy steel is used in cars, buildings, and big machines. These steels can take a lot of force and hits. Carbon steel is best for strong parts that do not need to fight rust. Alloy steel is picked for parts that must last and work hard.
Copper Alloys
Copper alloys include bronze and brass. They move electricity and heat very well. They do not rust easily and are simple to shape. These alloys are used for wires, pipes, and decorations. Copper alloys also wear well, so they are good for moving parts. Their shiny color and smooth look are nice for art and jewelry.
Nickel and Cobalt Superalloys
Nickel and cobalt superalloys are special. They can take very high heat and do not rust. These alloys are used in jet engines, turbines, and medical parts. In World War II, investment casting made blades and engines from these alloys. This let people make tricky shapes with high accuracy. Nickel and cobalt superalloys cost more. But they are needed for parts that face a lot of heat and stress.
Other Materials
Some companies use rare materials for special parts. These include titanium, magnesium, and glass. Ceramics are used to make the molds, not the parts. Ceramic molds help make smooth and detailed parts. Wax is covered with ceramic to make the mold. Some industries use glass or ceramics for parts that must fight heat or chemicals. These materials help make exact and special shapes.
Tip: Investment casting can make parts close to their final shape. It works with many alloys, even hard ones. This cuts waste and saves money. Robots and machines help make the process faster and better.
Investment casting materials give engineers lots of options. Each metal or alloy is good for different jobs. The best choice depends on what the part must do and where it will be used.
Properties and Applications
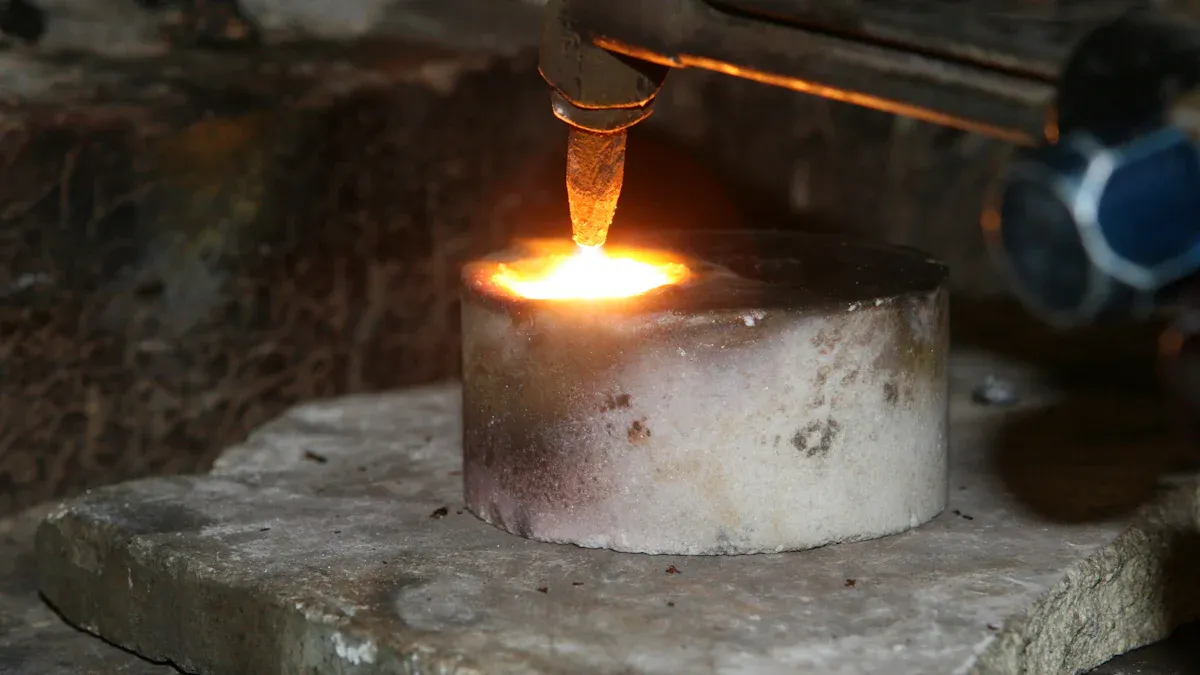
Mechanical Properties
Metals and alloys in investment casting have many mechanical properties. These help engineers pick the best material for each part. Titanium alloys like Ti64 can get weaker in thick parts. They may lose over 15% of their strength after long use in high heat. This happens when the grains inside the metal get bigger. Bigger grains make the part weaker. The table below shows how wall thickness changes the strength of Ti64 after 500 hours at 200–300°C:
Wall Thickness | Tensile Strength Loss (%) | Reason for Change |
---|---|---|
Thin | Low | Small grain growth |
Medium | Moderate | Some abnormal coarse grains |
Thick | >15 | Large grain coarsening |
Engineers look at this data to choose alloys that stay strong. Investment casting makes parts with great detail and tight measurements. This helps create parts that are both strong and detailed.
Corrosion Resistance
Corrosion resistance is very important for many cast parts. Metals like stainless steel, nickel alloys, and titanium do not rust easily. They also resist damage from chemicals. Labs test this using methods like ASTM C1617. In these tests, metal samples sit in harsh chemical solutions. Scientists check how much weight the metal loses. This shows the Mass Loss Corrosion Rate. They use math tests to make sure the results are good. Other tests, like the Neutral Salt Spray test, make corrosion happen faster. This helps see how metals do in tough places. These tests help companies pick metals that last longer in wet or salty spots.
Typical Applications
Many industries use investment casting for different reasons. Each industry picks metals and alloys that work best for them. The table below shows some common uses:
Industry | Materials Used | Applications | Key Benefits |
---|---|---|---|
Automotive | Aluminum, steel, copper alloys | Engine parts, chassis, gears | Lightweight, strong, precise |
Medical & Healthcare | Titanium, cobalt-chromium alloys | Implants, surgical tools | Biocompatible, custom fit |
Aerospace & Defense | Superalloys, titanium | Turbine blades, engine parts | High strength, heat resistance |
Industrial Machinery | Steel, specialty alloys | Machine parts, valves | Durable, complex shapes |
Oil & Gas | Specialty alloys | High-pressure components | Corrosion resistance |
Electronics | Copper, specialty alloys | Connectors, precision components | Fine details, surface quality |
Investment casting helps make parts with tricky shapes and smooth surfaces. Many industries need this process for high detail and good surface finish. It is used when parts must fit together well or work in hard places.
Comparison Guide
Material Performance
Different metals and alloys have their own strengths. Titanium, stainless steel, and nickel-based superalloys are very strong. They also resist heat and corrosion. Titanium investment casting makes parts with high tensile strength. These parts are between 860 and 1070 MPa. Titanium metal injection molding, or TiMIM, can reach the top of this range. TiMIM parts are less brittle and bend more before breaking. They also have more even quality. Investment casting is good for big or tricky shapes. TiMIM is better for small and detailed parts. Stainless steel does not rust and works in wet places. Nickel-based superalloys can take high heat. They are used in jet engines and turbines. Copper alloys move electricity well and do not wear out fast. They are used for electrical and moving parts. Each material group is picked for certain jobs in making metal parts.
Property | Investment Casting (MPa / %) | TiMIM (MPa / %) |
---|---|---|
Ultimate Tensile Strength (UTS) | 860 – 1070 MPa (125 – 155 ksi) | Up to 1070 MPa (155 ksi) |
Yield Strength (YS) | 758 – 965 MPa (115 – 140 ksi) | Up to 965 MPa (140 ksi) |
Elongation | 8% – 18% | Up to 18% |
Reduction of Area | 14% – 40% | Up to 40% |
Note: Investment casting can get dirty from ceramic shells or wax. This can lower part quality. TiMIM has less risk of this and gives more even results.
Cost Considerations
The material you pick changes the price and waste. Aluminum and carbon steel are cheaper and easy to shape. Nickel and cobalt superalloys cost more but last longer in hard jobs. Investment casting uses more material than TiMIM. This is because of sprues and ceramic shells, which make extra waste. TiMIM makes parts with less waste and uses less energy. But it only works for small parts made in large numbers. For big or special parts, investment casting costs less. Companies must think about price, waste, and how many parts they need.
Selection Tips
Engineers use tips to choose the best material for investment casting. They look at what the part needs, like strength, heat, and rust protection. For nickel-based superalloys, models like the Niyama criterion help find and stop problems like shrinking or holes. These models help pick the right metal and ceramic mold. Good molds must be strong and stable in heat. They also must not react with the alloy. New ways, like additive manufacturing, make molds more exact and lower mistakes. By using these tips, engineers can make better parts with fewer problems.
Picking the best metals and alloys for investment casting helps make parts that are strong, exact, and not too expensive. Each material works best for certain jobs. Stainless steel is good because it does not rust. Aluminum is chosen when parts need to be light. Superalloys are used in planes. Copper alloys are common in electronics.
- Engineers should:
- Look at what the part must do
- Talk to experts or suppliers about casting
- Make sure the material fits the job
Using the right investment casting material makes parts work better and last longer.
FAQ
What makes certain metals and alloys suitable for investment casting?
Some metals and alloys are better for investment casting. They flow easily and melt at lower temperatures. Their properties stay the same when heated. Stainless steel does not rust. Aluminum alloys are light but still strong. Nickel-based superalloys can take a lot of heat. These things help make parts that are smooth and detailed.
Which metal is best for lightweight investment casting parts?
Aluminum alloys are the top pick for light parts. They are not heavy but are still strong. Engineers use them in planes, cars, and electronics. Aluminum lets you make thin and tricky shapes. This makes it great for detailed castings.
Why do industries choose stainless steel for investment casting?
Stainless steel does not rust and stays strong. It is used for tools and equipment in food, medical, and marine jobs. It looks clean and lasts in tough places. Stainless steel is picked when parts must be safe and last a long time.
When should engineers use nickel or cobalt superalloys in investment casting?
Nickel and cobalt superalloys work well in very hot places. They are used in planes and power plants for engine parts and blades. These alloys keep their strength and do not rust, even when it is very hot or stressful.
Can copper alloys be used for investment casting in electrical applications?
Yes, copper alloys are good for electrical uses. They move electricity and heat very well. They also do not rust. Engineers use them for wires, connectors, and moving parts. Copper alloys last long and work well in both electrical and mechanical systems.