Selecting the optimal casting method for tractor casting parts depends on factors such as cost, precision, production volume, and the complexity of the component. Many manufacturers choose die casting for tractor casting parts due to its cost efficiency per unit and its ability to produce intricate shapes. For tractor casting parts that require high dimensional accuracy and a smooth finish, investment casting is often preferred, as it minimizes the need for additional machining. Sand casting is ideal for larger or simpler tractor casting parts and offers flexibility for design modifications. The table below outlines the typical cost range for each casting process when producing tractor casting parts:
Casting Method | Average Cost Range (USD per piece) | Notes on Cost Factors |
---|---|---|
Sand Casting | $6.60 – $6.80 | Highest cost, flexible for large parts |
Investment Casting | $3.20 – $6.00 | Good accuracy, saves machining costs |
Die Casting | $1.50 – $1.90 | Most cost-effective for high volume |
KEMING is a trusted manufacturer of tractor casting parts, utilizing advanced metal casting processes and innovative techniques to deliver robust and reliable components for modern agricultural machinery.
Key Takeaways
- Sand casting works best for big, simple, or custom tractor parts. It does not cost much and is very flexible. But the surface is rough and not very exact.
- Investment casting gives very accurate and smooth parts. It is good for small or medium parts with hard shapes. It is best when parts need to fit tightly.
- Die casting is the quickest and cheapest way for many small or medium parts. It makes smooth parts, mostly with aluminum alloys.
- Picking the best casting method depends on size, shape, how many you need, and your budget. You need to balance cost, quality, and how long it lasts.
- KEMING uses new casting methods and checks quality well. They make strong and exact tractor parts for many needs and materials.
Tractor Casting Parts Overview
Essential Performance and Design Requirements for Tractor Casting Parts
Tractor casting parts are very important for farm machines. These parts need to be strong and last a long time. They must handle heavy weight and lots of shaking. They also face tough weather and dirt. Makers use materials like gray cast iron, ductile iron, and steel alloys. These materials are strong and do not wear out fast. Gray cast iron is good for engine housings and axles. It is tough, easy to shape, and stops vibrations well. Ductile iron is even tougher and can take hard hits. This makes it good for crankshafts and differential housings.
Key things tractor casting parts need are:
- High compressive strength so they can hold heavy loads.
- Wear resistance so they last longer and need less fixing.
- Good thermal conductivity to help cool engine and gearbox parts.
- Vibration damping to keep parts safe and make driving smoother.
- Rust resistance so they work well outside in wet places.
- Precise tolerances so all parts fit together just right.
Some common tractor casting parts are engine blocks, gearbox housings, transmission boxes, axle casings, and wheel hubs. These parts must stay strong when the tractor works hard. They should not crack or bend. New casting methods help make parts with the right shape and smooth surfaces. This means less extra work is needed to finish them. Makers also try to make parts lighter when they can. Lighter parts help tractors use less fuel and are easier to drive.
Note: Tractor casting parts must meet strict rules for quality. Good castings help keep tractors safe and working well. This means farmers spend less time and money on repairs.
Sand Casting for Tractor Casting Parts
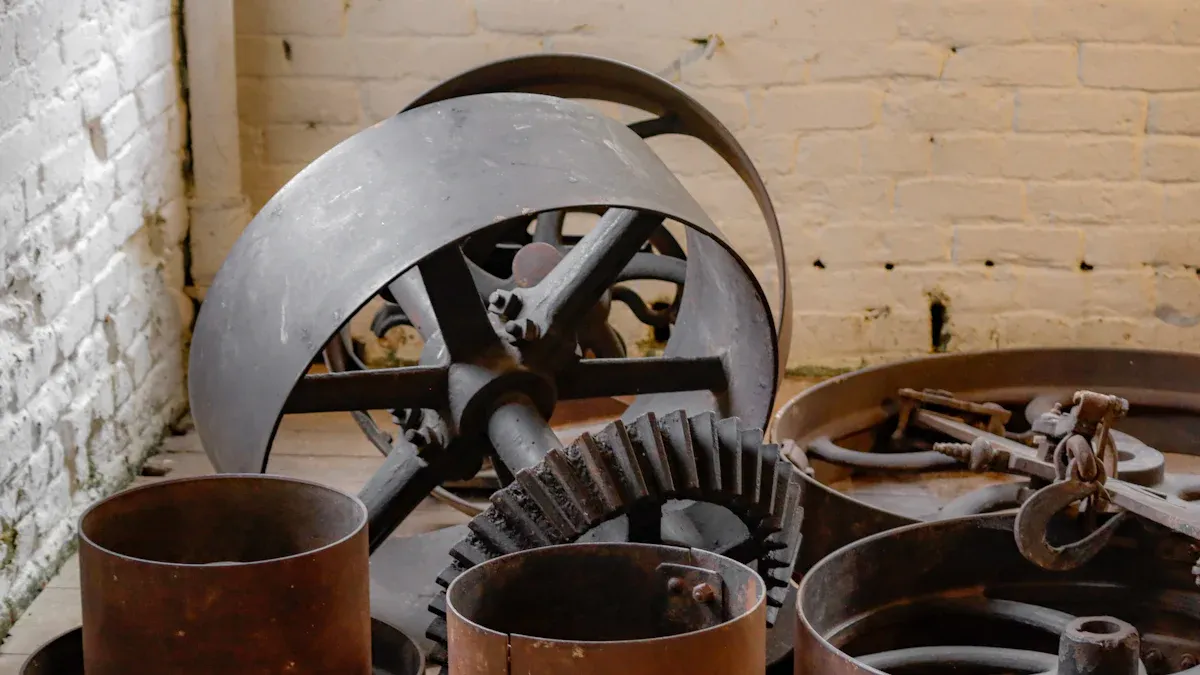
Overview of the Sand Casting Process for Manufacturing Tractor Parts
Sand casting is a common way to make tractor parts. In this process, sand forms a mold for the metal. The steps are simple and easy to follow.
- Pattern Creation: Workers make a pattern that looks like the part.
- Molding: They press sand around the pattern to form a mold.
- Melting and Pouring: Metal is melted and poured into the mold.
- Cooling and Solidification: The metal cools down and gets hard.
- Removal and Finishing: Workers break the mold and clean the part.
Sand casting can make big and complex parts. This makes it useful for many tractor jobs.
Advantages and Disadvantages of Using Sand Casting for Tractor Parts
Sand casting has many good points. It is great for making large and heavy parts. The process can shape parts that are hard to make in other ways. It is also easy to change the design if needed. This helps when making special or new parts.
But sand casting has some downsides too. The surface is not always very smooth. The parts may not fit as tightly as with other methods. For example, small parts can be off by about ±0.021 inches. Big parts can be off by about ±0.041 inches. The surface is usually about 80 microinches rough. These things are fine for most tractor parts that do not need to be exact.
Feature | Typical Value (Sand Casting) |
---|---|
Tolerance (small) | ±0.021 inches (±0.53 mm) |
Tolerance (large) | ±0.041 inches (±1.03 mm) |
Surface Finish | ~80 microinches (2.0 micrometres) |
Note: Sand casting is a cheap way to make strong tractor parts. The finish may not be perfect, but the parts last a long time.
Common Tractor Parts Manufactured Using Sand Casting Techniques
Many heavy tractor parts are made with sand casting. Axle assemblies are one example. These parts often break and are hard to fix by welding. Sand casting is a good way to make new ones. Other parts made this way are gearbox housings, engine blocks, transmission cases, and wheel hubs. Sand casting works well for these because it can handle big and tricky shapes.
Investment Casting in Tractor Casting Parts
Detailed Overview of the Investment Casting Process for Tractor Parts
Investment casting makes tractor parts with great detail and accuracy. This process uses many careful steps to make sure each part is just right. Here is how investment casting works for tractor parts:
- Tooling Making: Workers use CNC machines to make exact molds or patterns.
- Wax Injection and Pattern Assembly: Wax goes into the molds to make wax patterns. These wax patterns are put together on a sprue.
- Shell Building: The wax group is dipped in ceramic slurry and covered with sand. This step is done many times to make a strong ceramic shell.
- Dewaxing: The ceramic shell is heated to melt and remove the wax. This leaves a hollow mold.
- Casting: Hot metal is poured into the warm ceramic shell.
- Knocking Out: When the metal cools, the shell is broken off. The cast parts are taken off the sprue.
- Heat Treatment: The castings may be heated again to make them stronger.
- Surface Treatment: Workers may paint or coat the parts to protect them.
- Packaging: The finished parts are packed and sent to customers.
Investment casting can use many metals, like stainless steel and carbon steel. This method makes parts with tight tolerances and smooth surfaces.
Advantages and Disadvantages of Investment Casting for Tractor Parts
Investment casting has many good points for tractor parts. It can make shapes that other methods cannot. The process gives very accurate sizes and smooth surfaces. This means less extra work is needed. Investment casting works with many alloys, so it is flexible for different parts. It is best for small to medium amounts because tooling costs less than die casting.
But there are some downsides too. It does not work well for very big or heavy parts. The process takes more time and needs special tools. Tooling costs are higher than sand casting, and it takes longer to finish each part.
Aspect | Investment Casting Advantages | Investment Casting Disadvantages |
---|---|---|
Precision | High dimensional accuracy and intricate details | N/A |
Surface Finish | Smooth finish reducing post-processing | N/A |
Complex Geometries | Capable of producing complex and delicate shapes | N/A |
Cost | N/A | Higher tooling and material costs |
Size Limitations | N/A | Less suitable for very large parts |
Lead Time | N/A | Longer production cycle |
Production Volume | Best for low to medium volumes | N/A |
Tractor Parts Commonly Produced Using Investment Casting Techniques
Many tractor parts are made with investment casting. This method is great for parts with tricky shapes and fine details. Some examples are gear housings, hydraulic parts, brackets, and engine parts. These parts often need to fit very well and have smooth surfaces. Investment casting is also used for parts in combines, balers, planters, and plows. The process works with many materials, like stainless steel, carbon steel, and aluminum alloys.
Investment casting helps make strong tractor parts that last in tough farm work. The ability to make complex shapes with high accuracy makes this process a top choice for important parts.
Die Casting for Tractor Casting Parts
The Die Casting Process for Manufacturing Tractor Parts
Die casting uses high pressure to push hot metal into a steel mold. This mold is called a die. The process makes strong tractor parts fast. Here are the main steps:
- Workers close the two die halves with a press.
- A machine shoots melted metal, like aluminum, into the die. The metal cools and hardens quickly.
- The die opens, and pins push out the finished part.
Important tools include a piston, gooseneck, die, clamp, plunger, and pins. There are two types of die casting: hot chamber and cold chamber. Hot chamber machines heat metal inside the machine. Cold chamber machines melt metal in a separate furnace first. Tractor parts usually use cold chamber die casting. This is because aluminum alloys need more heat to melt.
Die casting is fast and can make detailed shapes with high accuracy.
Advantages and Disadvantages of Die Casting for Tractor Parts
Die casting has many good points for tractor parts:
Aspect | Advantages | Disadvantages |
---|---|---|
Production Speed | It is quick, saves money, and works well for many parts. | Starting costs are high, so it is not good for small jobs. |
Quality | Parts can have smooth surfaces and thin walls. | Small holes inside the part can make it weaker and harder to treat with heat. |
Dimensional Quality | It gives accurate sizes and smooth finishes. | The size of the machine and mold limits how big the part can be. |
Part Complexity | It can make strong, light, and complex parts. | Not all alloys or very large tractor parts can be made this way. |
Die casting is great for making finished parts that need little extra work. But it costs a lot to start and cannot make every size or use every material.
Typical Tractor Parts Manufactured Using Die Casting Techniques
Many tractor parts are made with die casting. Aluminum alloys are used a lot. They are light, strong, and do not rust easily. These alloys also help move heat away from the part. Some common die cast tractor parts are:
- Axles
- Chassis parts
- Counter mounts
These parts must be strong and not too heavy. Die casting helps make detailed parts with smooth surfaces. It is also good for the environment because aluminum can be recycled. Zinc alloys are used for smaller parts that need to keep their shape.
Die casting is a great way to make many tractor parts that need to be strong, exact, and smooth.
Comparison of Sand, Investment, and Die Casting
Cost
Cost is very important when picking a casting method for tractor parts. Each method has different things that make it cost more or less. These include the price of tools, materials, and workers. The table below shows how sand casting and investment casting compare:
Cost Driver | Investment Casting | Sand Casting |
---|---|---|
Tooling Costs | High starting cost because of wax patterns and ceramic molds; molds are used once, so each part costs more. | Lower tool costs; patterns can be used again, so it saves money over time. |
Material Costs | Material costs are higher, but there is less waste because parts are close to the final shape. | Material costs are lower, but there is more waste because molds are not as exact and more work is needed after casting. |
Labor Costs | Labor costs are higher because skilled workers and careful steps are needed; some machines can help. | Labor costs are lower because the process is simple and does not need special skills; more work is done by hand. |
Production Volume | Better for making lots of parts because the tool cost is spread out; good for tricky, exact parts. | Best for small numbers or big, simple parts; low starting cost makes it good for small jobs. |
Die casting costs a lot at first for the mold, but it is the cheapest way when making many parts. Die casting is fast and makes the same part over and over, so each part costs less when making thousands. Sand casting is best for small amounts or very big parts. Investment casting is good for medium amounts when you need both good price and accuracy.
Note: Picking the right casting method helps save money and gives the best value for each tractor part.
Precision
Precision means how well parts fit together and work smoothly. Each casting method gives different levels of accuracy and surface smoothness.
Casting Process | Dimensional Tolerance Grade | Typical Surface Finish (Ra, μm) |
---|---|---|
Sand Casting (Sodium Silicate) | CT12 – CT14 | 25 – 50 |
Investment Casting (Silica Sol) | CT5 – CT6 (most precise) | 1.6 – 12.5 |
Die Casting | CT5 – CT7 | Not given, but smoother than sand casting |
Investment casting is best for making very exact parts with smooth surfaces. Silica sol investment casting gives the tightest fit, so it is great for parts that must be just right. Die casting also gives good accuracy, especially for aluminum parts, and is fast for big orders. Sand casting is flexible but usually makes rougher parts that may need more work to be perfect.
- Investment casting helps tractor parts fit better and work well.
- More precise parts last longer and work better.
- Sand casting may need extra work after casting to meet strict rules.
Material Compatibility
The metal needed for a tractor part helps decide which casting method to use. Each method works best with certain metals.
Casting Method | Compatible Materials | Typical Applications for Tractor Parts | Limitations |
---|---|---|---|
Sand Casting | Cast iron, steel, aluminum, copper, brass | Big, heavy, tricky parts like engine blocks, plough bodies | Rough surface, less accurate, slower, molds used once |
Investment Casting | Many metals (often non-ferrous alloys) | Small, detailed, thin-walled parts needing tight fit | Higher cost, harder process, best for small parts |
Die Casting | Aluminum alloys, zinc alloys, magnesium, brass | Lots of parts like gear housings, clutch covers | High mold cost, not as good for very tricky inside shapes |
Sand casting can use many metals, like cast iron and steel, which are common for heavy tractor parts. Investment casting is good for non-ferrous alloys and makes small, detailed parts. Die casting is best for aluminum and zinc alloys, so it is used for light, rust-proof parts.
Production Volume
How many parts you need affects which casting method is best. Die casting is best for making lots of the same part because it is fast and makes each part the same. This is great for mass production.
Investment casting is good for medium amounts, especially when parts need to be exact and have tricky shapes. Sand casting is best for small numbers or custom parts because it is cheap to start and easy to change designs.
Tip: For big orders of the same part, die casting saves time and money. For test parts or small jobs, sand casting is more flexible.
Surface Finish
Surface finish is how smooth a part is. Smoother parts work better and last longer because they have less friction.
Casting Method | Typical Surface Finish (Ra, μm) | Notes |
---|---|---|
Investment Casting | 1.6 – 12.5 | Very smooth, needs little extra work |
Sand Casting | 25 – 50 | Rough, often needs more finishing |
Die Casting | Not given, but smoother than sand casting | Good finish, often ready to use |
Investment casting gives a very smooth finish, so parts need less extra work and perform better. Die casting also makes smooth parts, especially with aluminum. Sand casting makes rougher parts, so they may need more work before use.
- Painting, coating, or shot peening can make parts last longer and stop rust.
- Smoother parts wear less and last longer in tough farm work.
Part Complexity
Complexity means how tricky the shape of a part is. New sand casting, like with 3-D printed sand cores, can make very tricky parts, even with thin walls and inside spaces. But tricky shapes may need special ways to finish and put together.
Investment casting is great for making detailed, thin, and tricky parts. It is the best way for parts that need exact shapes and fine details. Die casting can also make tricky shapes, but only if the part fits in the mold and uses the right metal.
- New fast casting methods, like moldless sand casting, let makers design more complex tractor parts.
- Old methods may limit size and detail, but new tech keeps making more things possible.
Durability
Durability means how well a tractor part can handle stress, wear, and tough use. Investment casting makes strong parts that last, especially for small, exact parts. Die casting also makes strong, stable parts, so it is good for making lots of parts that must last.
Sand casting is good for big, heavy parts and is not expensive, but the surface may not be as good and more parts may be thrown away. This can make the finished part less strong. Vacuum die casting and low-pressure casting can make die cast parts even stronger inside.
Note: Checking quality at every step makes sure tractor parts are strong and safe to use.
Choosing the Right Casting Method for Tractor Parts
Matching to Part Needs
Picking the best casting method for tractor parts depends on what you need. Each method is good for different reasons. The table below shows which method fits each need best:
Criteria | Sand Casting | Investment Casting | Die Casting |
---|---|---|---|
Material Type | Works with many metals | Good for high melting alloys and many metals | Best for non-ferrous metals like aluminum and zinc |
Part Complexity | Makes tricky shapes | Very precise, great for thin and detailed parts | Good for simple shapes and lots of parts |
Dimensional Accuracy | Okay accuracy | Very accurate (CT4 to CT7) | Very accurate and smooth |
Production Volume | Good for small or big batches | Best for small to medium batches | Great for making lots of the same part |
Cost | Cheap tools, saves money | Costs more for better detail | Cheap for big orders |
Mechanical Properties | Wears well, easy to machine | Strong against heat and wear | Strong and smooth for non-ferrous metals |
Surface Finish | Not super smooth | Very smooth | Very smooth |
Example Tractor Parts | Gearboxes, brake drums, pulleys | Detailed, tricky parts | Parts that need to be smooth and made in bulk |
Tip: Use investment casting for parts with thin walls and tricky shapes. Sand casting is good for big, simple parts. Die casting is best for making many smooth, matching parts.
Budget and Scale
How much money you have and how many parts you need matter a lot. Each casting method works best for different project sizes and budgets:
- Sand casting is cheapest for tools. It is good for small batches or big, heavy parts. You can change the design easily.
- Investment casting costs more but gives very exact and smooth parts. It is best for medium batches or when you need tight fits.
- Die casting costs more at first for the mold. But it is cheapest when you make thousands of the same part. It is fast and needs little extra work.
Production Scale | Best Method | Why Choose It? |
---|---|---|
Prototype/Small | Sand Casting | Cheap, easy to change, flexible |
Medium | Investment Casting | Very exact, good for tricky parts |
Large/High | Die Casting | Fast, cheap for big batches, smooth finish |
Note: Think about how many parts you need and how exact they must be. Die casting is best for lots of parts. Investment casting is better for special or tricky parts.
KEMING’s Solutions for Tractor Part Casting
KEMING is a top company for farm casting parts. They use many casting methods, like investment casting, shell mold sand casting, lost foam casting, and lost wax casting. These ways help KEMING make strong, rust-proof tractor parts that fit well and look smooth.
KEMING uses special casting to make detailed parts that are very exact. This means less extra work and less wasted metal. They use many metals, like stainless steel, carbon steel, alloy steel, grey iron, ductile iron, and aluminum. These metals help tractor parts work well in tough farm jobs.
KEMING also offers special finishes, like shot blasting, polishing, heat treatment, sandblasting, and coatings. These finishes make parts last longer and stop rust and wear. With over 20 years of work and ISO 9001 certification, KEMING makes strong, high-quality castings for every tractor job.
KEMING helps from design to making the part. Their skill in casting helps farmers and builders get the right parts, making machines work better and break down less.
Picking the best casting method for tractor parts depends on size, shape, and how many you need. Sand casting is good for big or simple parts. Investment casting is best for detailed parts that must be exact. Die casting is great when you need many parts with smooth surfaces. KEMING uses new casting technology to help customers. Their team helps people pick the right method for each job. For the best outcome, talk to KEMING’s experts.
FAQ
What is the most cost-effective casting method for large tractor parts?
Sand casting is the best choice for big tractor parts. It uses simple molds and is good for large shapes. Many makers pick sand casting to save money on strong, heavy parts.
Which casting method gives the smoothest surface finish?
Investment casting makes the smoothest surfaces. This process gives parts fine details and little roughness. Makers use investment casting for tractor parts that need a shiny, clean look.
Can die casting be used for all tractor parts?
Die casting is best for small or medium parts made from aluminum or zinc. It is not good for very big or heavy tractor parts. Most large parts use sand casting or investment casting instead.
How does KEMING ensure the quality of tractor casting parts?
KEMING checks quality at every step. The team looks at raw materials, checks molds, and tests finished parts. These steps make sure each tractor part is strong and lasts a long time.
What materials are common in tractor casting parts?
Makers often use gray iron, ductile iron, carbon steel, and aluminum alloys. Each material has its own strengths. Gray iron stops shaking well. Aluminum alloys are light and do not rust.